ピースピッキングにもロボット活用、従業員数大幅減
「RDC」とはRegional Distribution Center(大型物流センター)の略称。敷地面積は約67,000平米(約2万坪)、床面積は約45,000平米(14,000坪)。2018年8月に稼働した「RDC新潟」と比較すると、規模は出荷額ベースで約5倍と、PALTAC最大規模の物流センターとしてオープンする。年間出荷額は1,200億円を想定している。立地は埼玉県北葛飾郡杉戸町で、首都圏中央連絡自動車道(圏央道)幸手インターチェンジから車で約8分の場所。首都圏の流通を担うには最適だという。配送エリアは埼玉、千葉、東京、栃木、茨城、群馬の関東エリア。投資総額は230億円。内訳は土地39億円、建物96億円、設備96億円。取り扱いアイテム数は2万SKU。
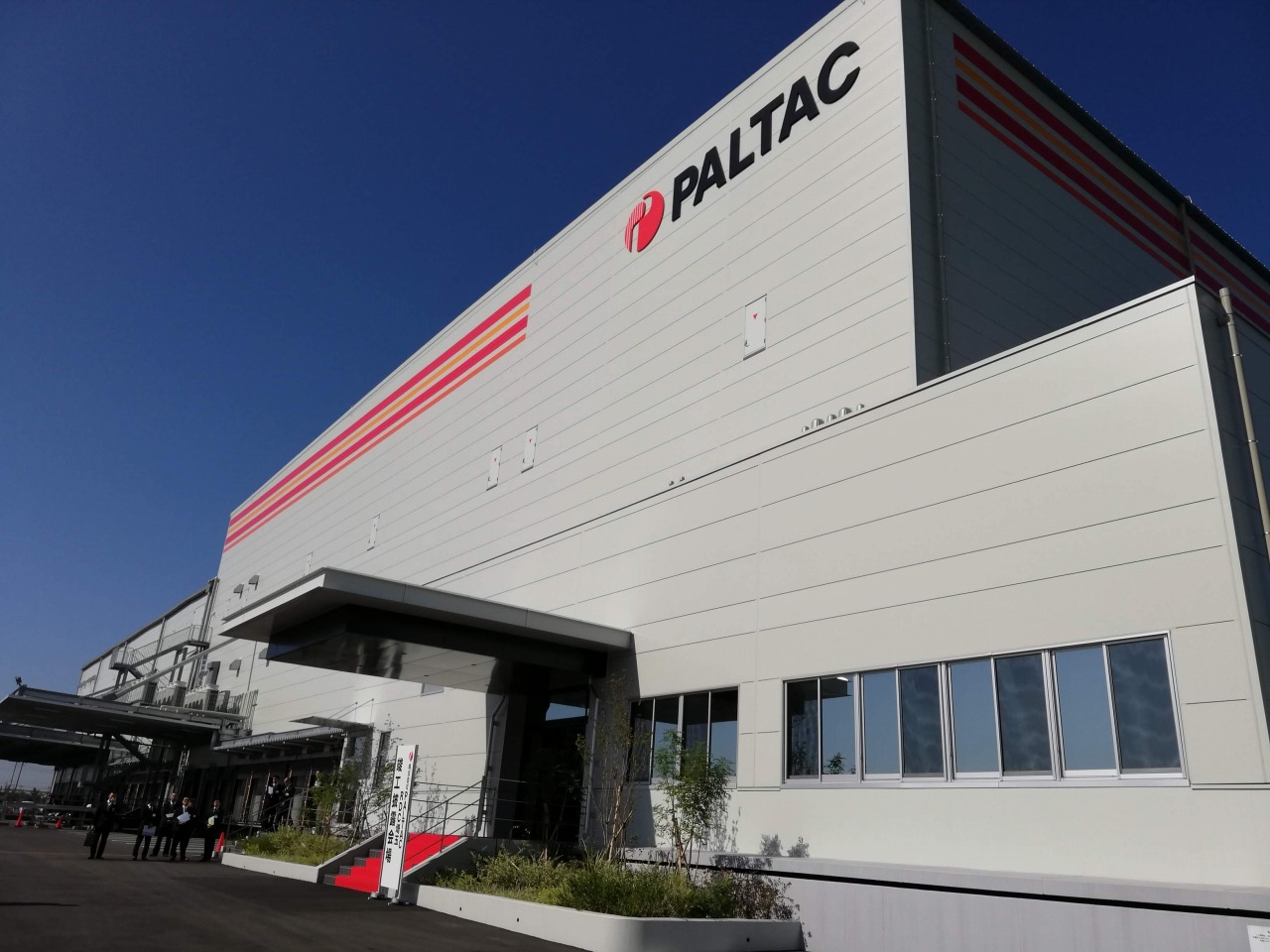
RDC埼玉でもRDC新潟同様、人が歩かないバラピッキングシステム「MUPPS(Multitaskcrane Piece Picking System、マップス)」を活用している。加えて最大の特徴はさらなる生産性を追求するため、ロボットの適用範囲を拡大したこと。RDC新潟ではケースピッキング(デパレタイズ)のみにロボットを活用したが、それに加えてケースローディング(積み付け)、ピースピッキングにもロボットを活用する。人とロボットを組み合わせることで、「バラ出荷」の人員生産性は従来のセンターの2.5倍となった(RDC新潟では2倍)。初期投資効率は新潟の2倍になるという。「ケース出荷」も含めたトータルの生産性は2.3倍を想定している。

人員数で見ると、RDC埼玉ではパート従業員300名が常時作業するが、従来の方式なら800名規模になるという。入庫エリアにも「自動入庫検品システム」を導入し、ドライバーの荷下ろし時間を大幅削減する。設備の投資額は従来のセンターに比べると「十数億円くらい高い」が、3年程度でペイするとのこと。維持費は従来のセンターと変わらず約1億円。
PALTACでは卸の枠を超えて自社で技術開発を行っているが、今回は3Dビジョンを活用したモーションプランニングによる知能ロボットソリューションを提供するスタートアップ3社と協業している点も特徴だ。会見にはピースピッキングを自動化したRightHand Robotics, Inc.、ケース積み付けを自動化した株式会社MUJIN、ケースハンドリングを自動化したKyoto Robotics株式会社の3社も同席し、それぞれの強みとソリューションを紹介した。
さらに進化した次世代型物流システム「SPAID」
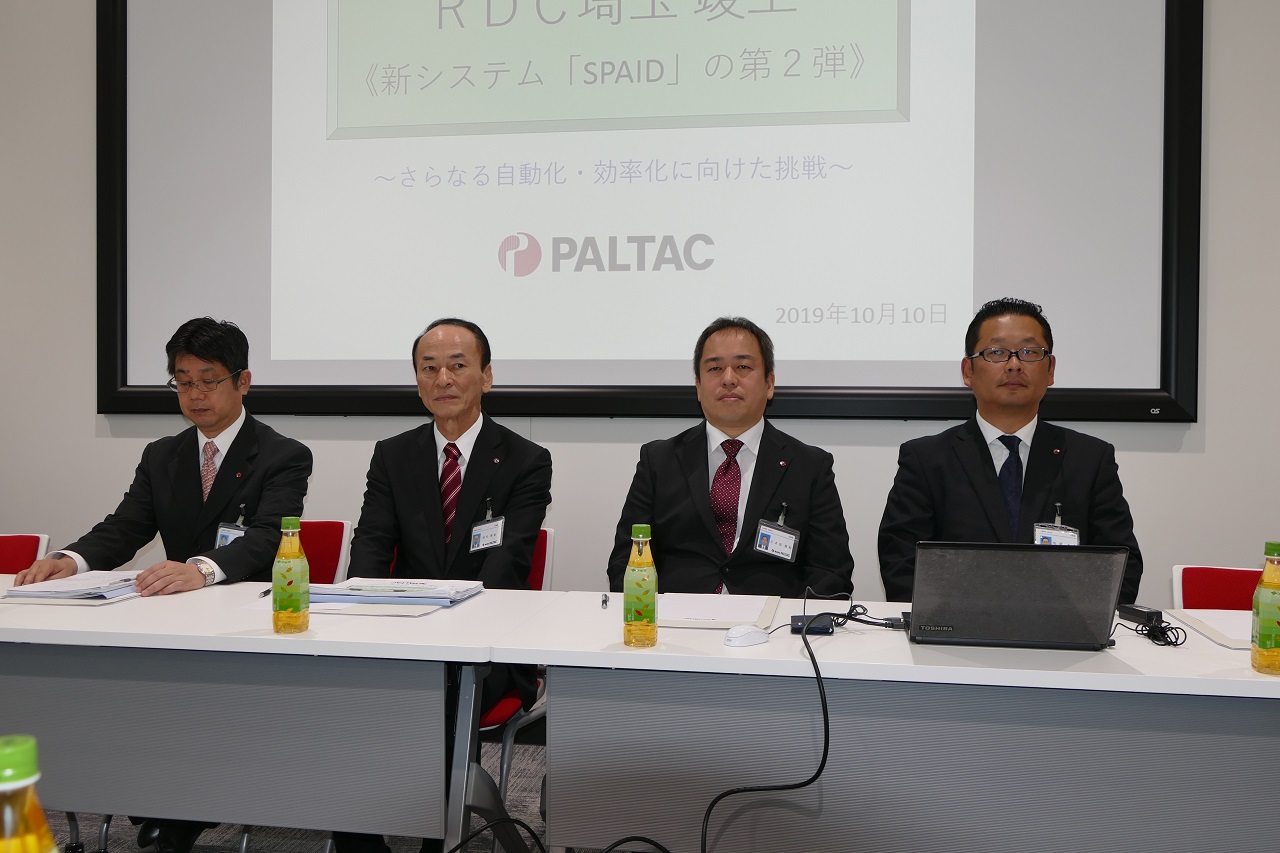
物流センターでは常時2万種類以上の商品を在庫し、毎年1万種類近い商品が入れ替わる状況にある。PALTAC取締役専務執行役員 物流・情報システム統括本部長の田代雅彦氏は、生産性の向上と、サプライチェーン全体を視野に入れた「ホワイト物流」について強調した。ロボットのほかに自動入庫検品システムと、作業人員の適正配置を可能とする入庫予約システムを組み合わせることで、トラック着荷時間が平準化。これによってトラックの待機時間を短縮した。また、フォークリフト作業を排除するなどして安全性も増すこともできたという。
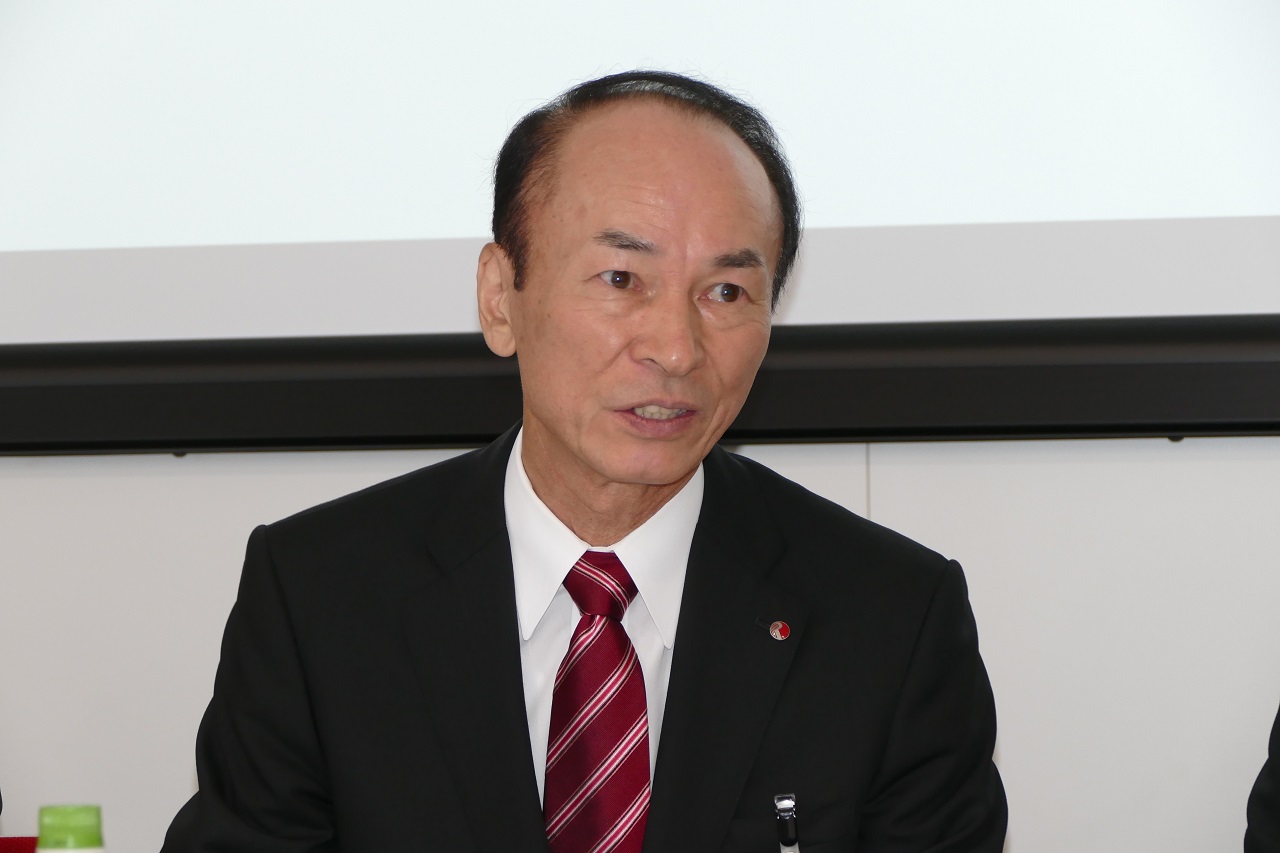
物流センターの物の流れは、ダンボールケースのまま入庫・出荷する「ケース物流」と、ケースの中の物品を一度バラして個別に必要分を組み合わせて出荷する「バラ物流」に大別される。今回は、その両方にロボット技術を導入した。RDC埼玉での内訳は、全体の出荷作業量のうちバラ出荷が7割程度を占める。
[ケース出荷の流れ]重筋作業から人を解放
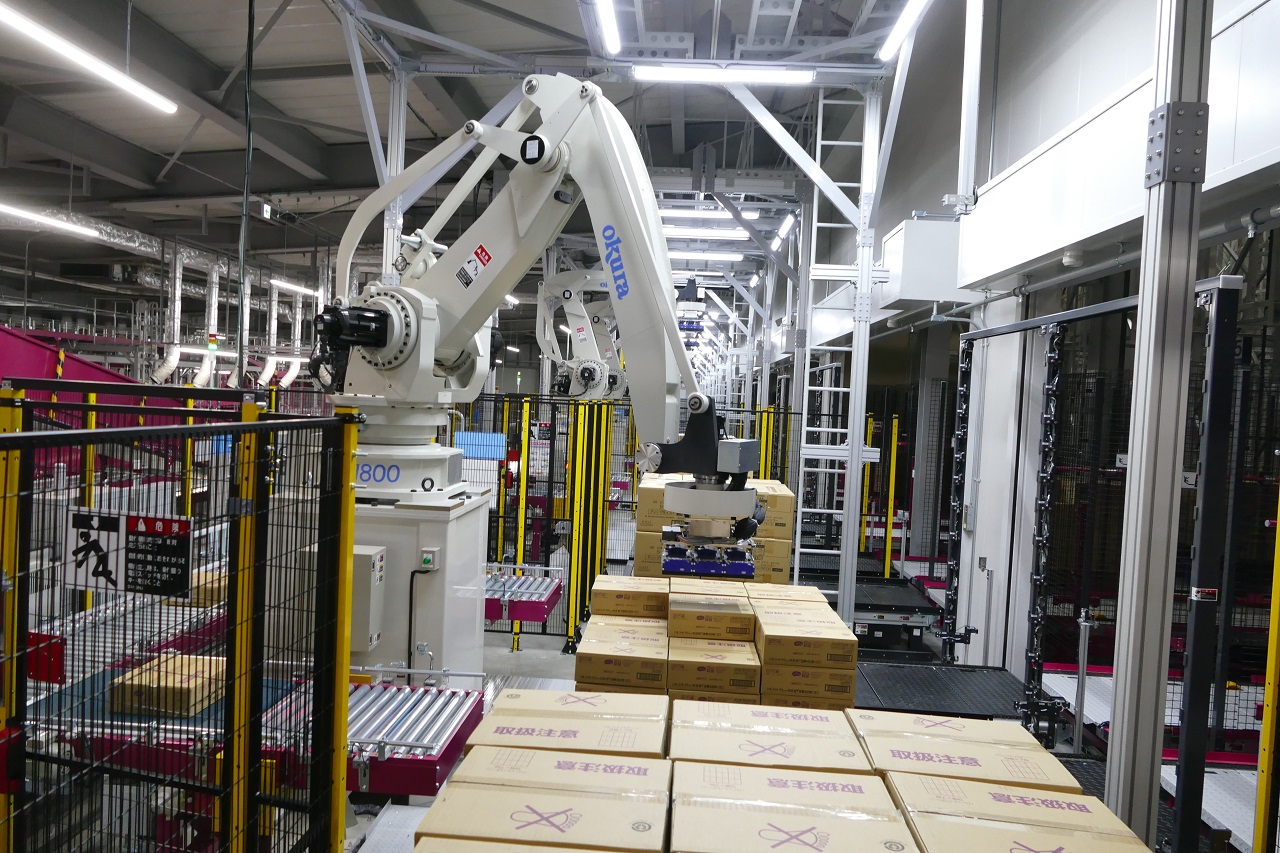
まずはケース入荷・出荷の場合は、入荷したケースは、「自動入庫検品システム」を経て、最適速度に制御されてパレットを安定搬送できる自動台車「ロボストレージ」で自動的にパレット自動倉庫へ送られる。これによってフォークリフトによる入庫がなくなった。ケース単位入荷商品はケース自動倉庫に送られる。出荷時は、それぞれの自動倉庫から「ケースピッキングロボット」を使って、ケース積み付けシステムを経由して作業者によって出荷されるか、そのまま出荷される場合は「ケースシーケンサー」に一時格納されて積み付け順に順立てて出庫し、「ケースローディングロボット」を使って店舗別に出荷されていく。
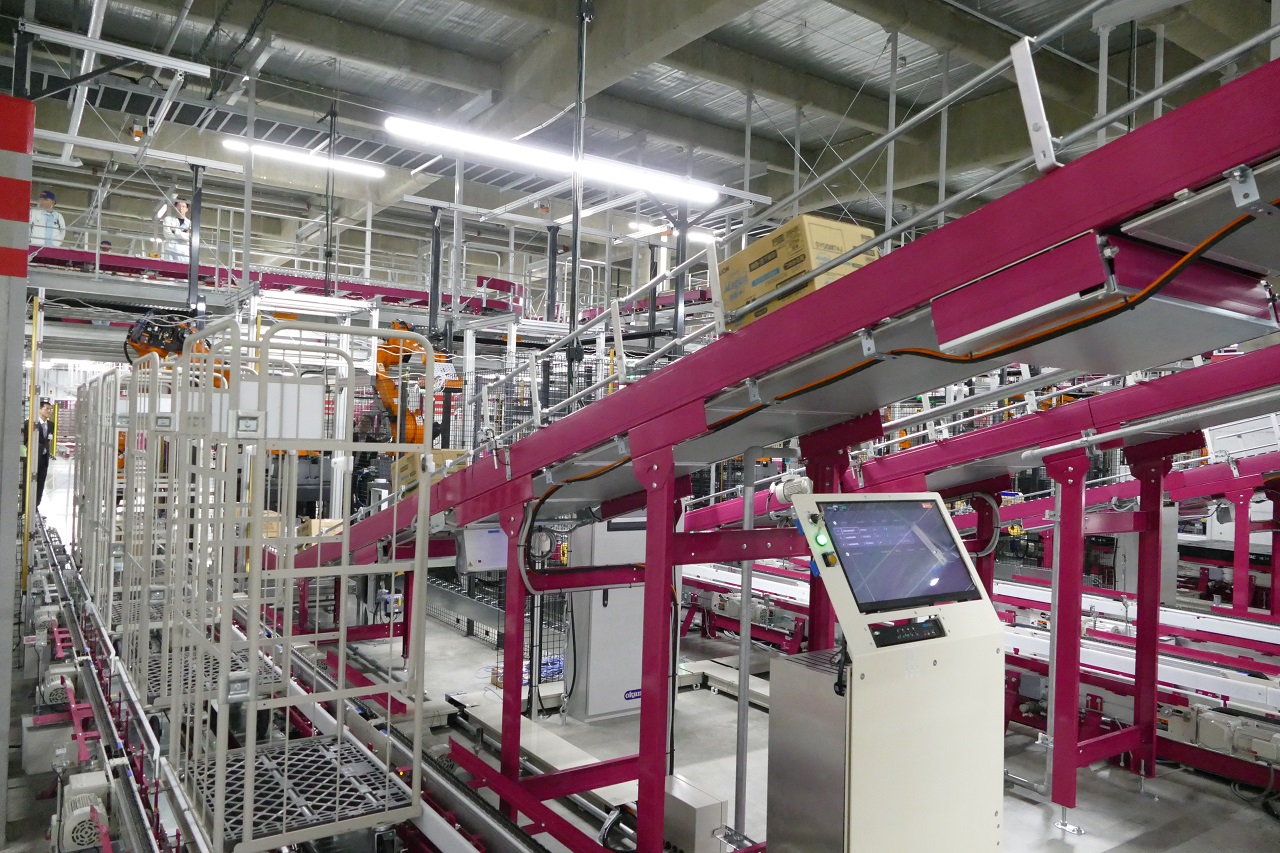
ケースピッキングはケース認識率を 99.8%まで向上させた。マスター登録をする必要がなく事前測定作業の必要もない。ピック速度は平均で1時間あたり700ケースで、これは世界最速だという。しかも出荷ミスがゼロになった。ロボットは同時に寸法と重量を計測し、そのデータも一緒に後工程に送られて活用される。
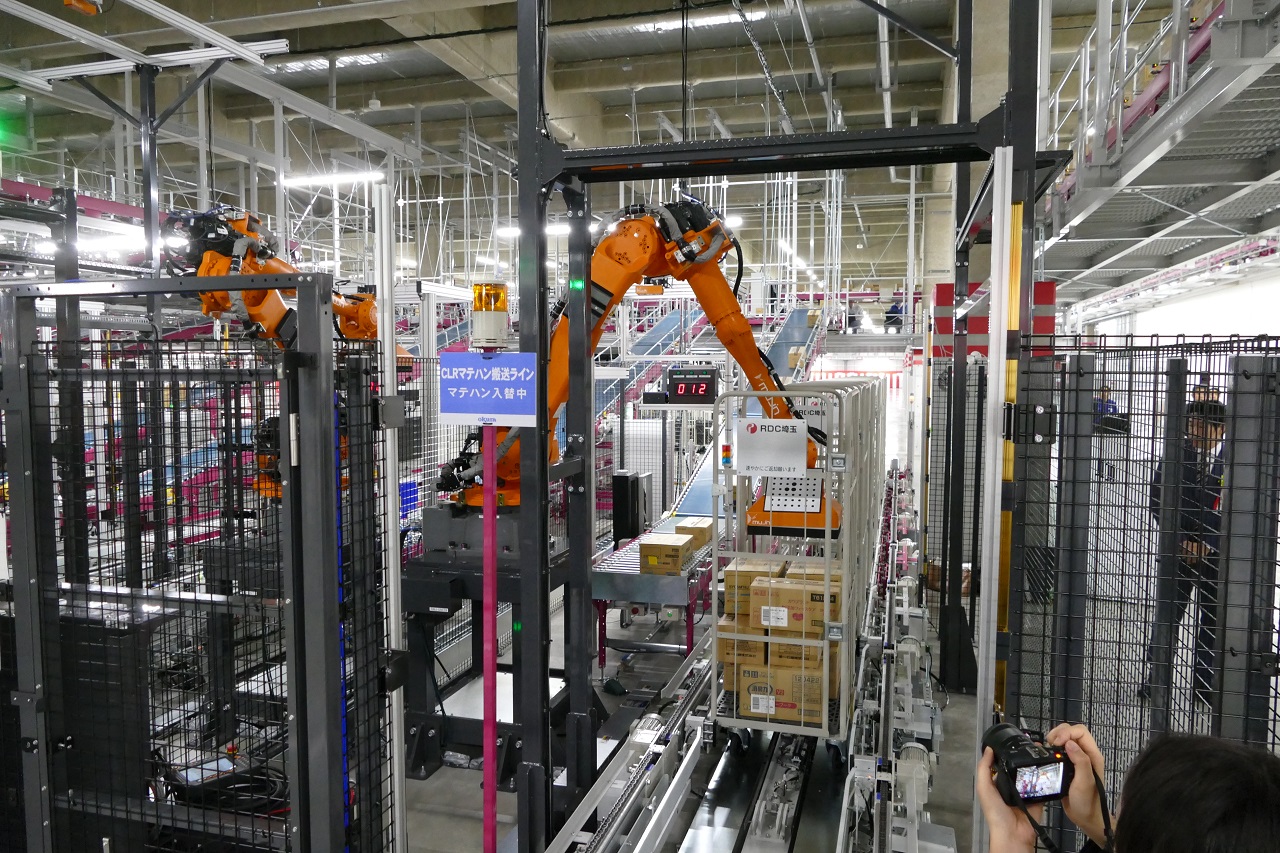
「ケースシーケンサー」には最適充填アルゴリズムを搭載しており、後工程で各種マテハン機器に積み付けを行うケースローディングロボットが扱いやすい順番でケースを出庫する。これにより人手での積み直しがなくなり、ロボットはパレット、かご車、カートラックなど3種のマテハン機器にケースを自動積み付けするが、人手よりも高効率な積み付けができるという。積み付け速度は最大で1時間あたり450ケースで、世界最速。人にとって負荷の高い作業を削減できると同時に、充填効率が最大となり、配送コストの削減が可能になった。
作業者がパレットに積み付けを行うときは「E-ELS」という作業者負荷軽減システムを用いる。パレットの高さを昇降装置で最適な位置にコントロールすることにより、常にほぼ同じ高さで積み付けすることで、作業者の腰の負担を大幅に軽減することができる。
[バラ出荷の流れ]人は歩かず、ロボットと組み合わせ
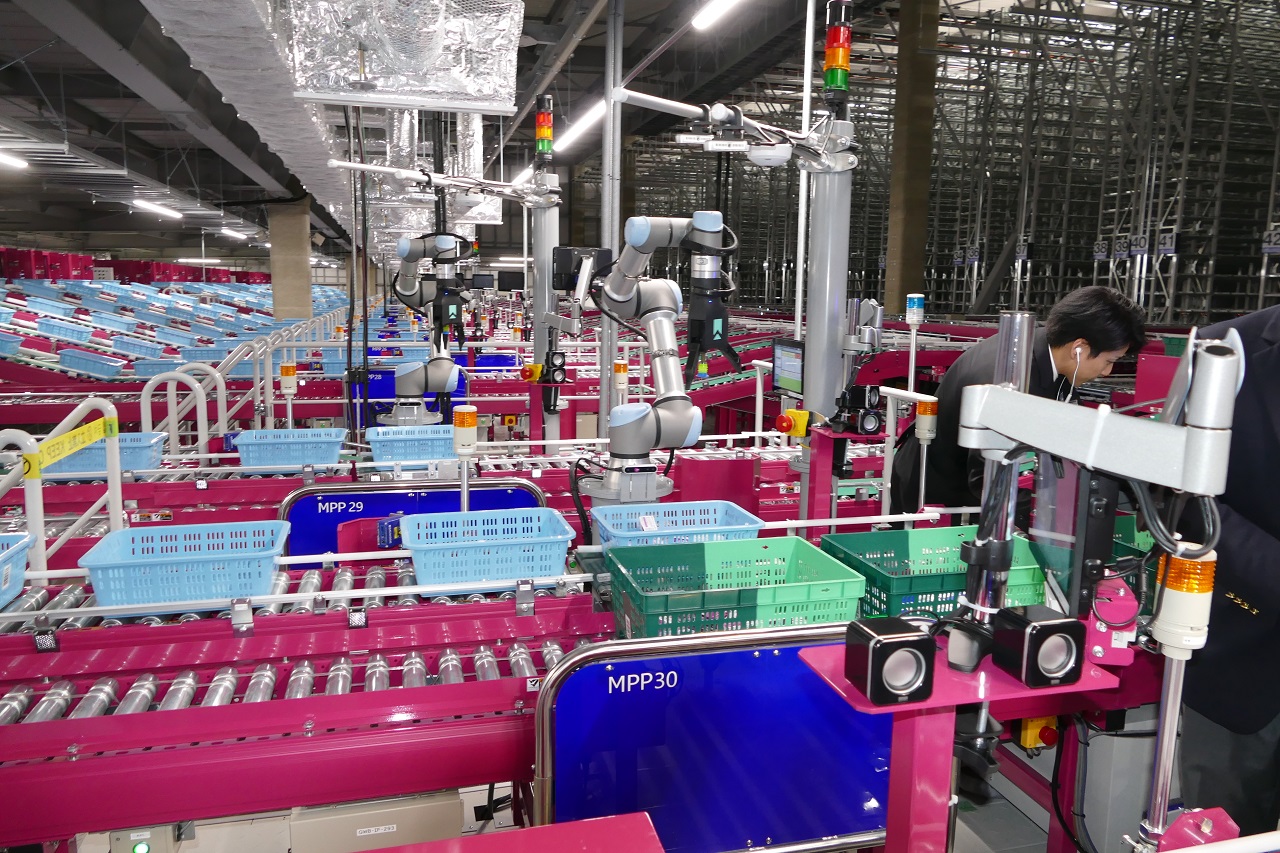
バラ出荷の作業は、効率よく出荷するために、ケース内の商品をストレージトレーステーションで保管トレーに移し替えるところから始まる。この過程にはまだ人手が使われているが、歩き回る必要はない。保管トレーはいったん自動倉庫へ自動搬送される。その後さらにピックトレーステーションで必要数量分を保管トレーからピックトレーに移し替える。ここの過程には、ロボットと人手が組み合わされているが、やはり人は歩いて商品をピックする必要はない。将来的にはすべてロボット化して完全自動化したいと考えているという。
商品を詰められたオリコンはクロスベルトソーターで搬送され、店舗ごとに割り当てられた間口に仕分けされる。そしてパックステーションでオリコンに詰め替え、オリコンシーケンサーで一時格納されてまた積み付け順に順立てされて出庫。そしてオリコンスタッカーかオリコン積み付けロボットによって積み付けられたあと、二度で結束バンドを取り付けられて出荷バースまで自動搬送され、出荷となる。オリコン積み付けロボットは3つのオリコンを把持して同時に積み付けることができる。生産性は3倍に向上した。
ケースの天面カットにはSSカッターまたはオートカートンカッターが用いられており、その後の蓋取り工程も完全自動化されている。これによって作業者負担と安全性が向上した。
既存設備は運用で改善
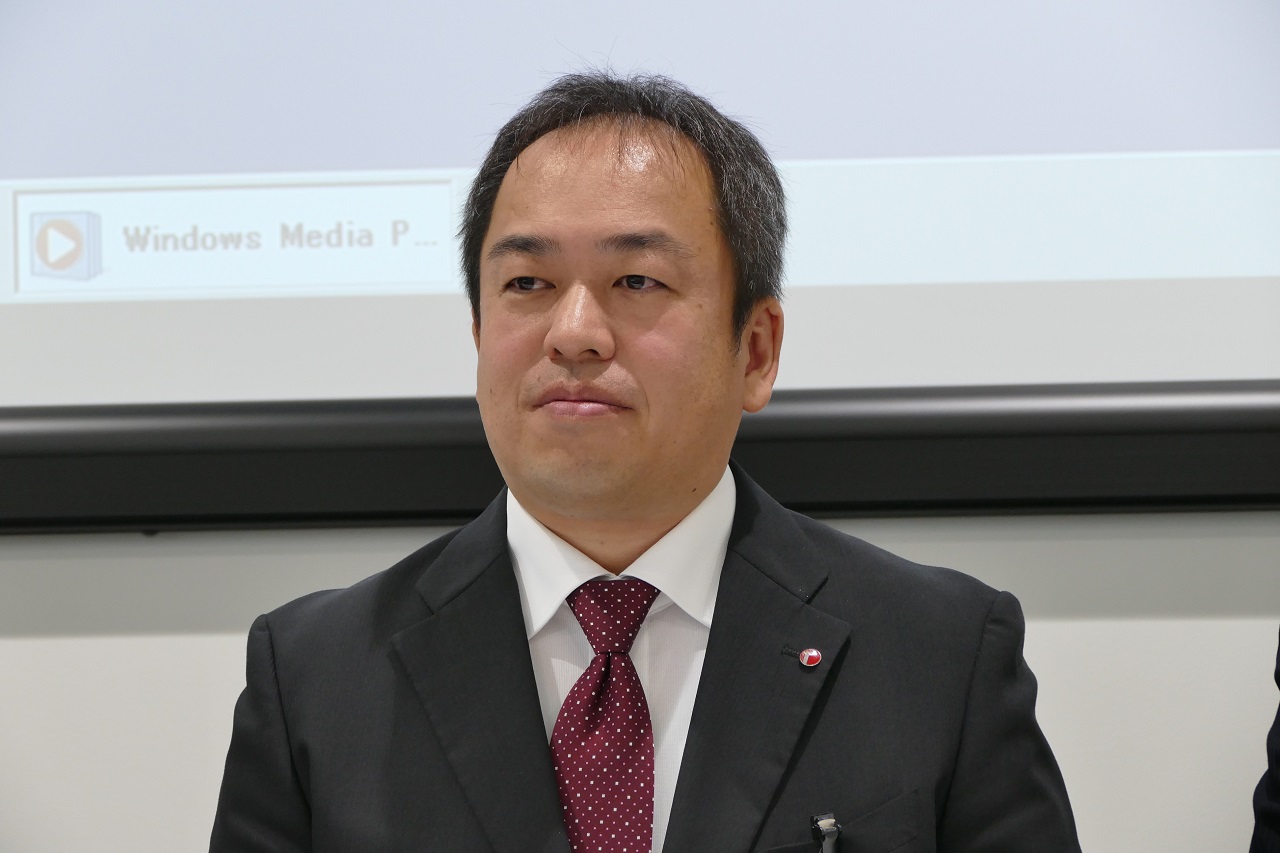
「RDC埼玉」の稼働時間は現状は15時間と見て最大出荷額1,200億円という計算になっている。だが自動化によってセンターの稼働時間を延ばすことができれば、出荷額も上げることができる。だがパート従業員の確保は困難になっており「取り合いのような状況」にある。そこで新技術活用による労働環境の良さをアピールしてパートの確保に務める。
生産性向上については、既存設備については「SPAID」は導入できないため、「RDC埼玉」のような仕組み自体を変えることによる生産性改善と、従来のセンターでの運用面での生産性改善を、並行して進めていく。なお、新センターを立ち上げたことによって、従来のセンターであっても活用できるヒントが得られるという。たとえば「歩かない」ということが生産性向上の鍵であることがわかったので、いかに歩行距離を短くするかをカギとして従来のセンターの改善を行なっていくとのこと。
PALTACではシステム担当者が100名、開発で20名が技術関連業務に従事している。全体のシステムはPALTACが設計しているが、今回の取り組みは前述のとおりスタートアップ3社と共同で行われている。今回スタートアップと組んだ理由は「特にスタートアップにこだわっているわけではないがAIやロボティクス領域の活用においてはスタートアップのほうが圧倒的に速度が速いからだ」とのことだった。
[ピースピッキング自動化] RightHand Robotics
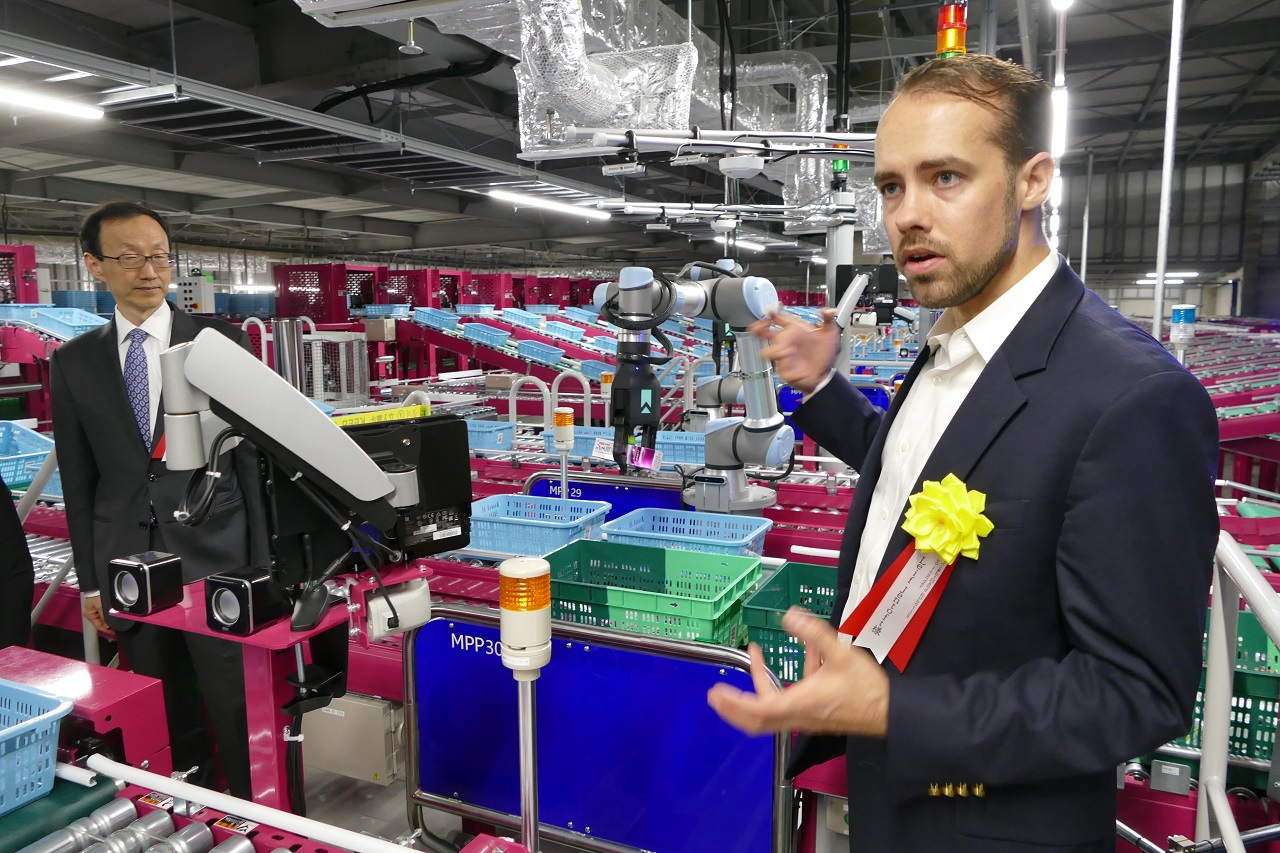
ピースピッキングの自動化には、2019年3月に協業を発表したRightHand Robotics, Inc.(RHR)のピースピッキングソリューション「RightPick2」を活用している。導入したロボットは10台。同社のco-founder(共同創設者)のLeif Jentoft氏は「PALTACは最先端のものの見方をする企業。未来のフルフィルメント拠点に携わることができてワクワクしている」と語った。「RightPick2」の国内導入は初めて。
RHRは2011年に米国DARPA(国防高等研究計画局)の主催するロボットマニピュレーションの競技会をきっかけに集まったチームをもとにした会社。「顧客課題に対応するソリューションを提供することで初めて世の中を変えることができる」と考えて起業したという。
アメリカでは従業員の無断欠勤が2割以上と大きな課題となっている。また物流センターでは離職率が非常に高く、300%にも及んでいるという。そこで自動化が求められているが、ピースピッキングの自動化は難しい。
RHRはカメラとロボットアーム本体は既製品を用い、手先のグリッパーと制御ソフトウェアは自前で開発している。グリッパーは物体を挟めるクリッパーと吸引が組み合わされた独自のデザインだ。また、ディープラーニングを活用し、過去の経験にもとづいて学習していく機能を搭載している。学習に必要なラベルデータは自動生成され、学習はクラウド上で行われる。
最大の特徴が、事前学習やスキャニングを必要としないモデルフリーアプローチの機械学習をとっているところ。事前にスキャンする必要がないので最初の設定が楽なだけでなく、包装が変わったり、特定シーズンのアイテムなどにも自在に対応ができる。なかには20万種類以上のアイテムをハンドリングしている顧客もあるという。
同社の技術は「Range(範囲)、Rate(速度)、Reliability(信頼性)」の3Rを掲げており、ケース内に高密度に物が入っていてもピックできるなど、様々な掴み方ができるとアピールした。また、日本が戦略的に重要なマーケットだと考えており、日本にも合同会社を設立したと田村研三郎氏を紹介した。Leif Jentoft氏は「ロボットをうまく活用してロジスティクスの世界をよりよくしたい。ロボットは顧客満足を最適化します」と語った。
PALTAC研究開発本部 副本部長 松本祥平氏は質疑に答えて「速度にこだわらなければおおよそ半数はピッキングできるが、ロボットが得意なアイテムとリトライが多いアイテムがある。そのグラデーションのなかでどこまで人で行い、どこまでをロボットでやるかは検討中」と述べた。
[ケース積み付け自動化]MUJIN
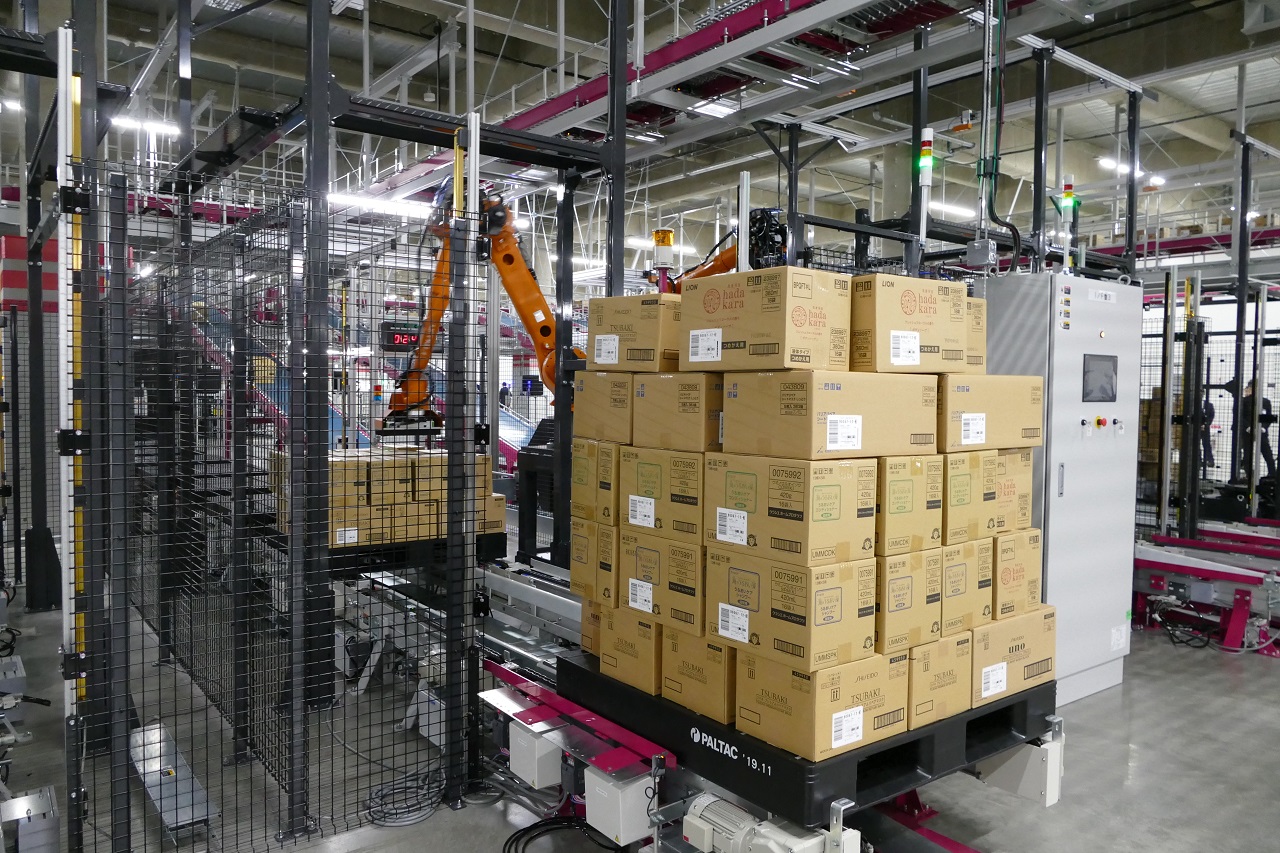
MUJINのロボット・パレタイズ・ソリューションも導入する(2019年6月発表)。出荷時のケース積み付け工程を自動化し、重労働を削減する。パレットやカーゴ車、カートラックなど出荷マテハンに対して最適な積みつけ位置を自動で決定し、ロボットが自動で積みつけていくことができる。積みつけ対象のケースの把持位置、搬送方法などの設定は必要ない。特に一つのロボットによる3種別以上のケース積み付けは従来は難しかったが、今回初めて実現する。
なおMUJINのソリューションは「RDC新潟」にも既に導入されている。RDC新潟ではパレット自動倉庫から出庫したケースを4台のロボットがパレットからおろしてコンベヤに自動投入している。
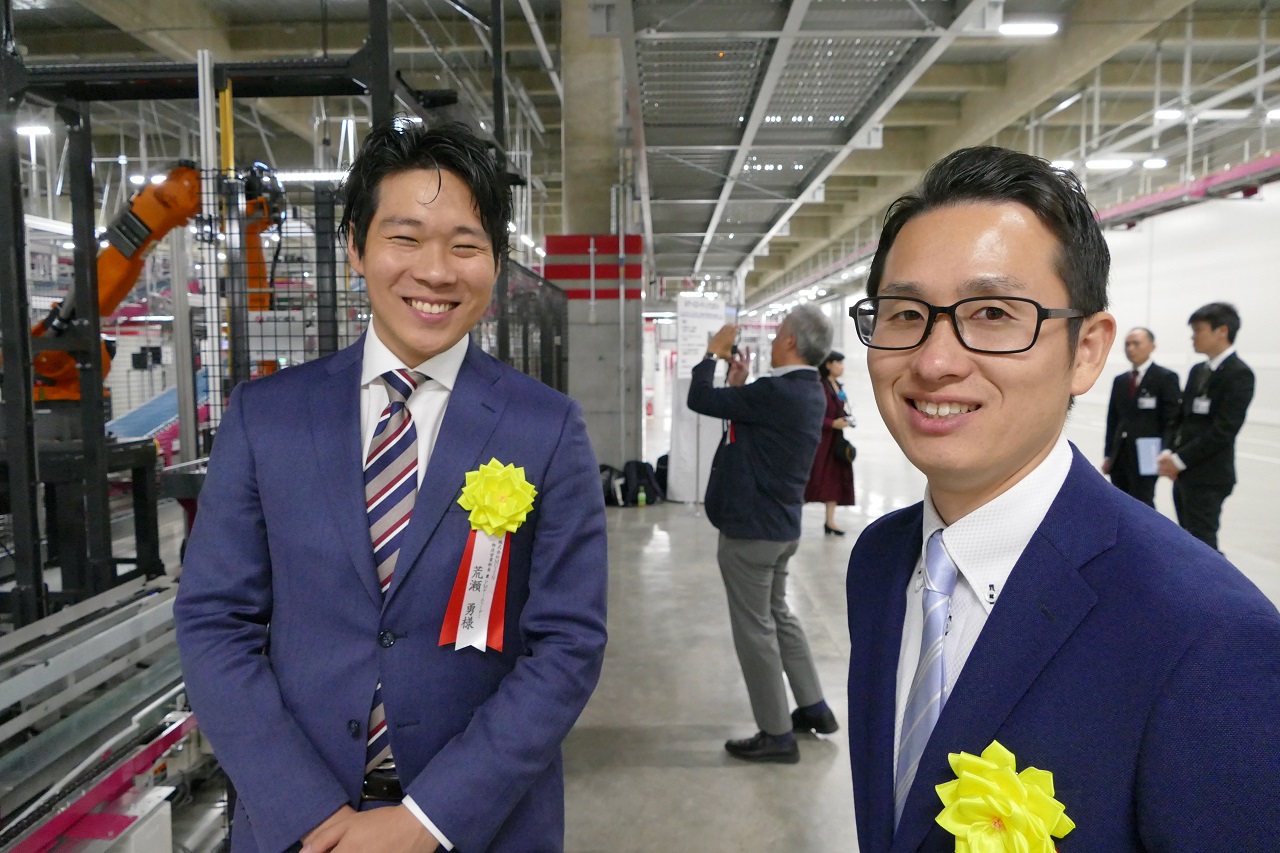
MUJIN CEO兼共同創業者の滝野一征氏は、PALTACについて「恩義がある会社だと認識している」と述べて「新しいチャレンジの機会を得て嬉しい」と語った。MUJINはロボットを制御する「コントローラー」を作っている会社だ。産業用ロボットはロボットメーカーごとに操作性が異なり、ティーチングも別々の方法を学ぶ必要がある。また基本的に繰り返し動作を実行するだけなので、柔軟性が必要な中間物流業者では使いづらかった。
MUJINのロボットコントローラーを使うと、事前のティーチング作業なしで多品種の物体をハンドリングできるようになる。現在8社の産業用ロボットに対応しており、物流は同社売り上げのうち60%を占めている。RDC新潟では単載のデパレタイジングをロボットで行なっているが、今回は混載を3種類の什器(パレット、かご車、カートラック)にロボットで積んでいる。。
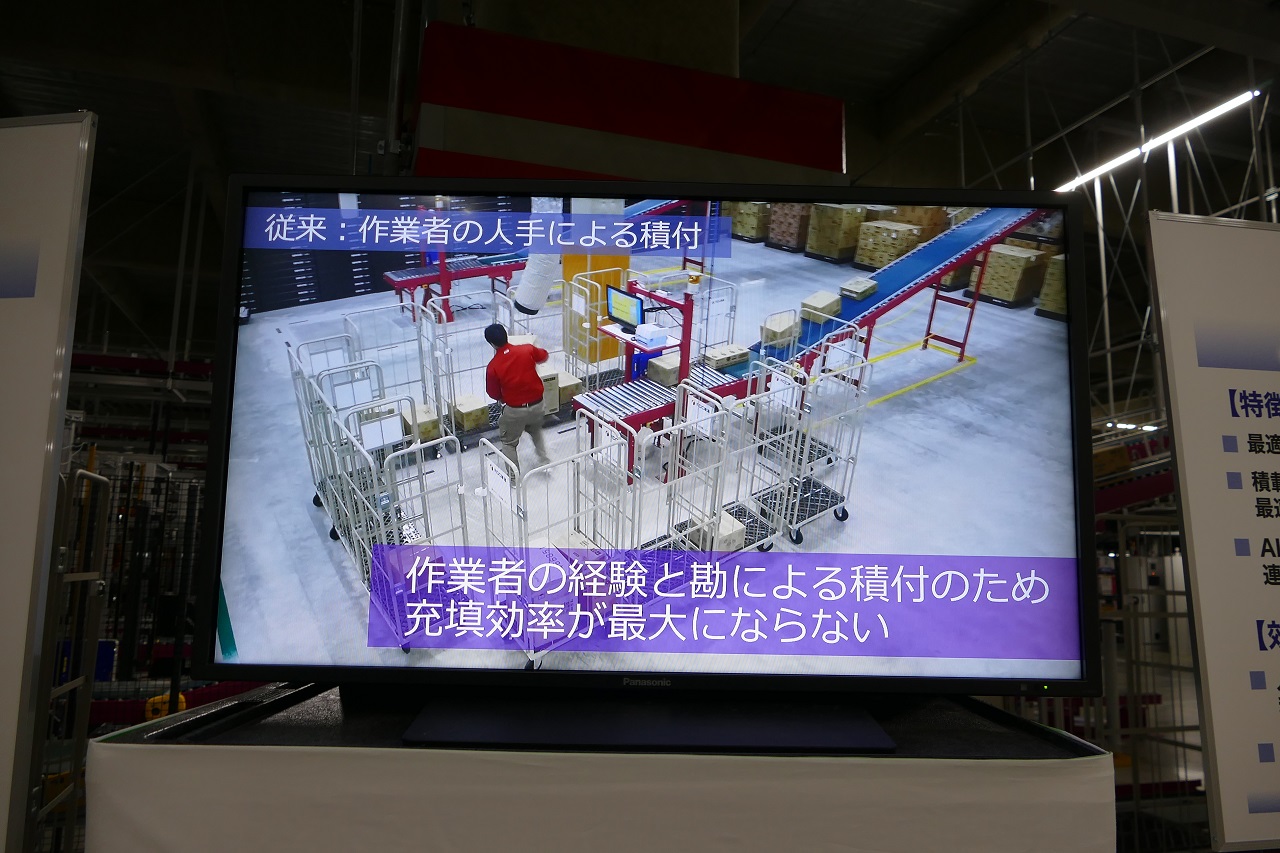
従来はシュートの下に人が、手作業で目的地に応じて箱を積み、必要に応じて積み直し作業を行なっていた。だがMUJINの技術によって、まず最終的に積載するロボットの動作まで考慮した積み付け計算を事前に行なってケースシャトルで順番立てが行われて、適切な順に箱が流れてくるようになった。単純に詰めばいいわけではなく、ラベルを外にして積んだり、上からドンと置くのではなく横からややスライデンィグして積載するといった動きをロボットが自動生成することができる。また、かご車が変形してることもありえるので、事前にカメラを使って什器を見て認識している。これらの技術によって非常に高い効率で重労働作業を自動化できたと述べた。滝野氏は「PALTACとMUJINが目指す世界は重筋作業がない世界」だと語った。
また前述のRightHand Roboticsのようなピースピッキングも中国JD.comでは行なっているとライバル意識を見せた。「ライバルが入ってくることは悪いことではない」と述べ、「MUJINの強みは様々なアプリケーションがあること。デパレだけ、ピースピッキングだけではなく、一気通貫で上流から下流までやってくれというときに応えられる会社だ。また全て自社のプラットフォームの上で動かしており、自分たちの制御システムで全てを握っている」と語った。
[ケースピッキング自動化]Kyoto Robotics
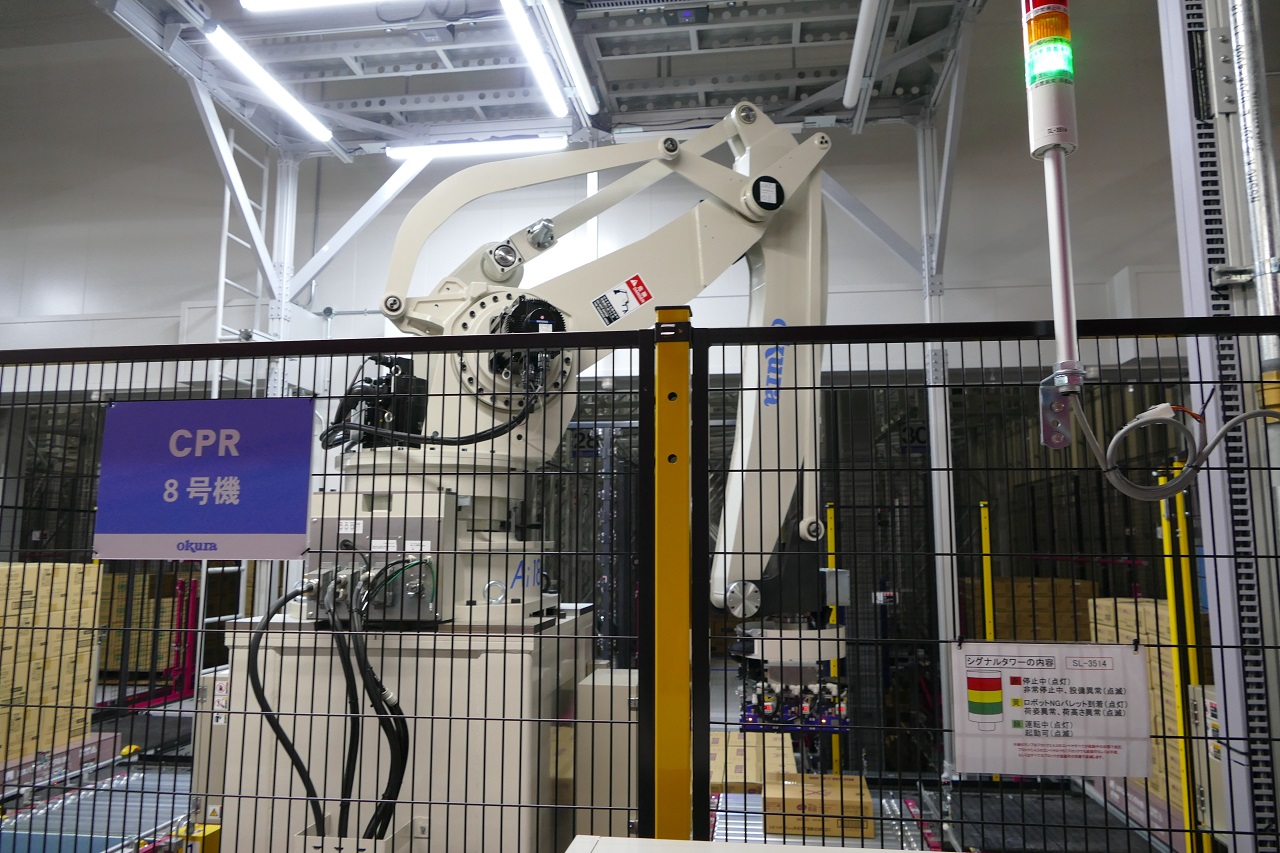
3次元ビジョン技術を活用したマスター登録不要の技術を使ってケースピッキングロボット(デパレタイジングロボット)を提供するKyoto RoboticsとPALTACは2019年5月に自動化パートナーとしての取り組みに合意していた。商品ごとにケースサイズや重量は異なるため、従来は導入初期や改廃の都度行なっていたマスター登録が必要だった。それが不要になり、ヒューマンエラーがなくなると同時に、時間あたり処理能力も向上した。
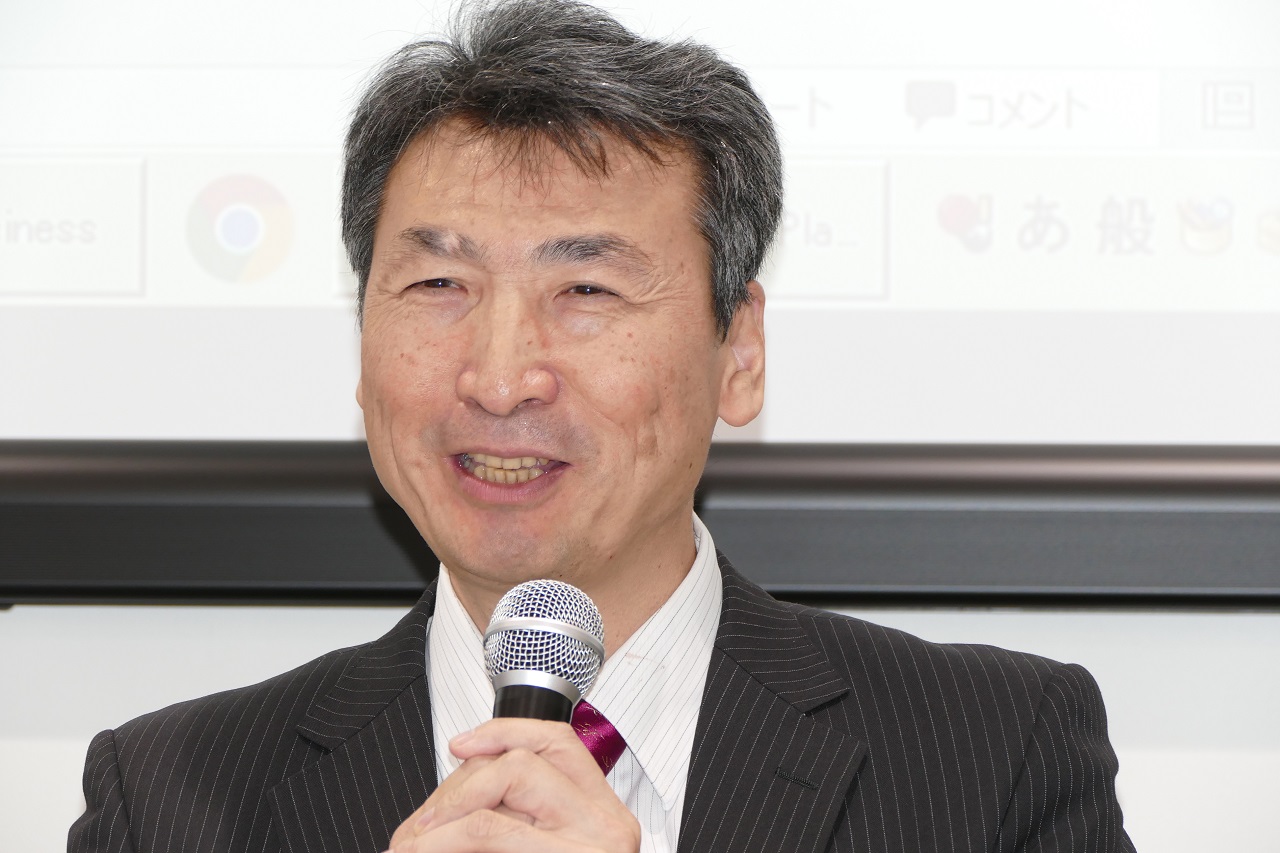
代表執行役社長の徐剛氏は同社について「3次元の目と脳を作っている会社だ」と紹介した。3次元ロボットビジョンセンサ「TVS」は、プロジェクタから特殊な模様を照射して高精度な3次元点群データを作ることができる。以前はビジョンセンサだけを提供しFA分野を主な対象としていたが、2017年からは物流分野に進出し、PALTACとの開発を続けてきた。
今回導入されたロボットは8台。1万4000個を収納するパレット自動倉庫から降りてきたパレットからのデパレ作業を行う。ハンドは一種類だけで、様々なケース天面形状を徹底研究して確実にピックできることを確認したという。速度は平均1時間あたり700ケース。ビジョンのパラメーター調整は必要ない。環境光にも非常に強く「倉庫のシャッターを開けたくらいではビクともしない」という。
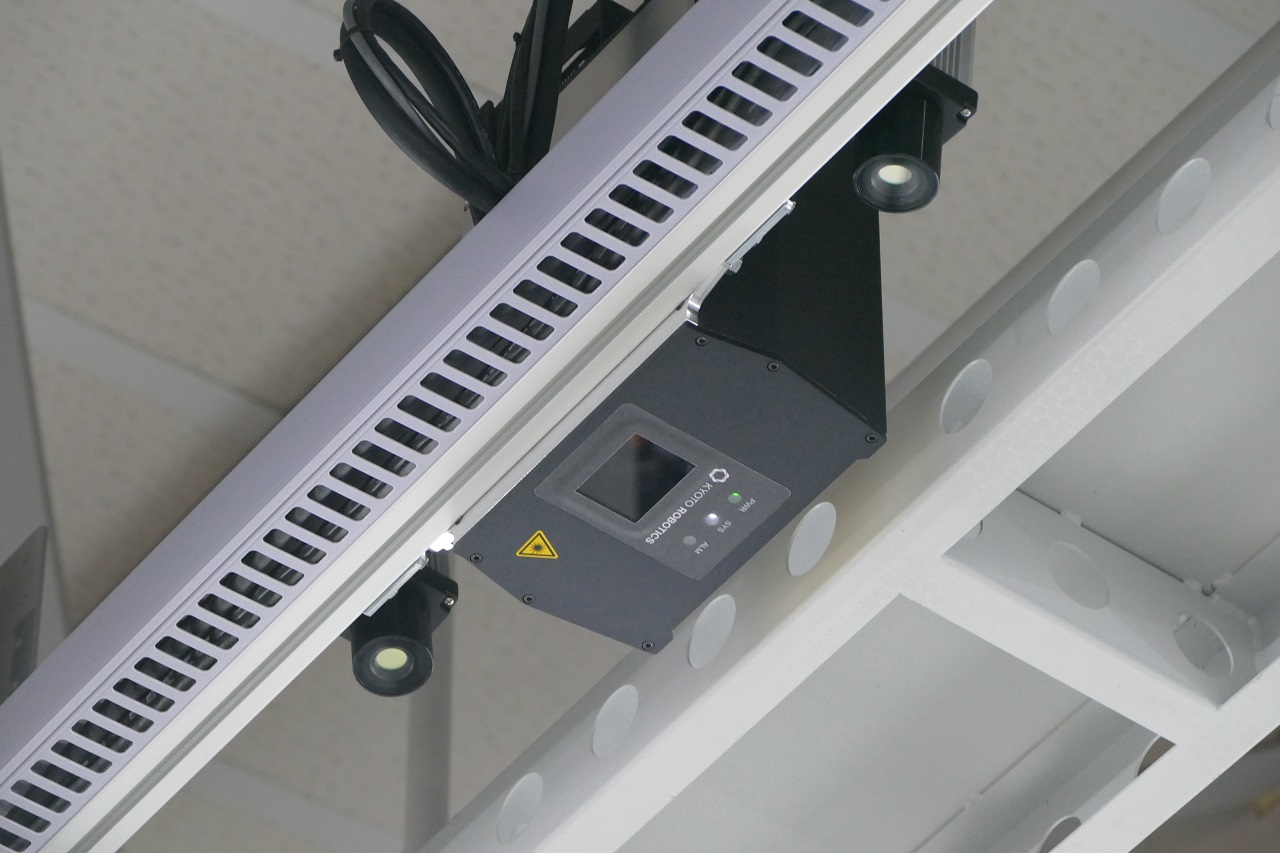
そのまま出荷される場合は、前述のMUJINのロボットが作業を行なっているケース積み付けに回る。Kyoto Roboticsのロボットは作業中にケースの寸法と重量を高精度計測する。MUJINはそのデータを使ってシミュレーションを行なっている。
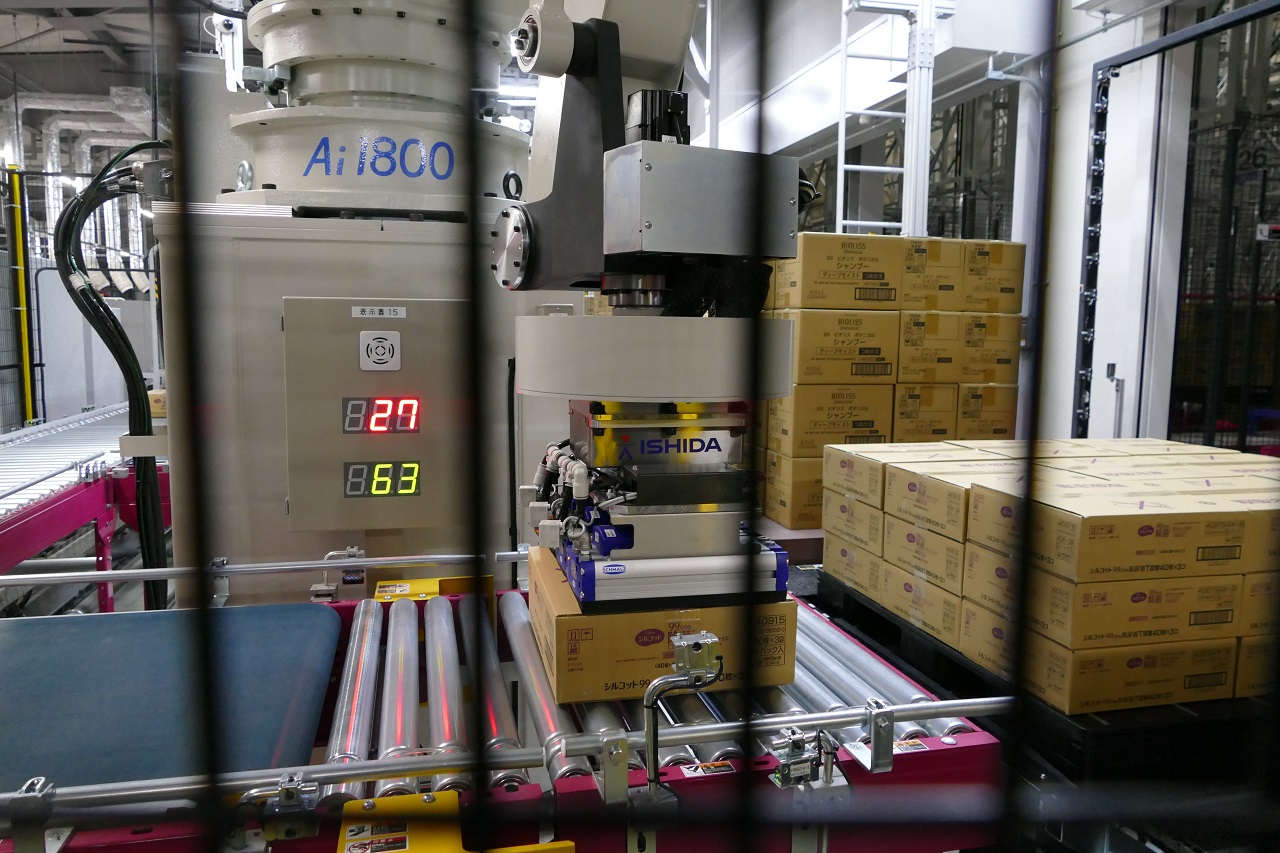
徐剛氏は、「アナログからデジタル、デジタルからアナログへいくところが難しい」と語った。「目は非常に厄介なアナログの光を相手にしている。そこからデジタルな認識をしないといけない。ハンドも力学や摩擦などアナログの要素が強い」ため難しいと課題を紹介した。今回は単載のデパレロボットだが、今後は混載のニーズにも応えていくという。