物流倉庫のイメージがひっくり返る!?
今日の案内役をつとめるのは本誌連載でもおなじみのPALTAC研究開発本部長の三木田雅和さん。前職では自動車メーカーでロボットエンジニアをしていたという異色の経歴の持ち主。
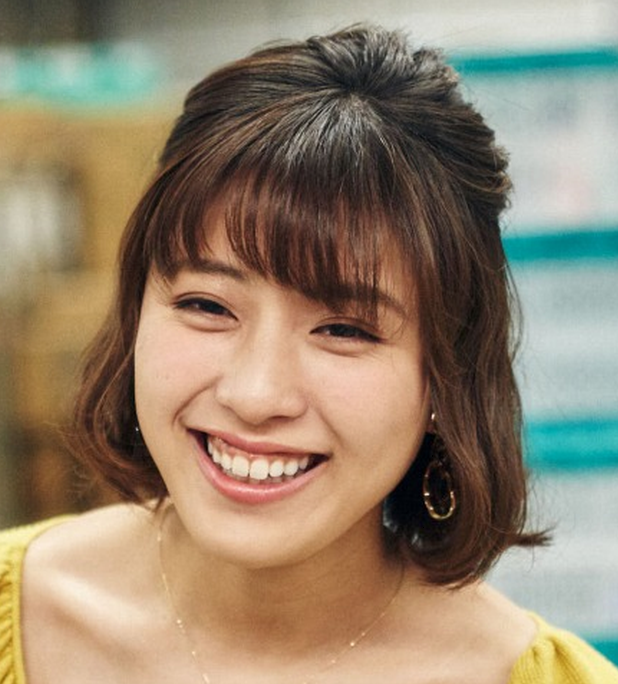
はじめまして!三木田さん。今日はよろしくお願いします!!
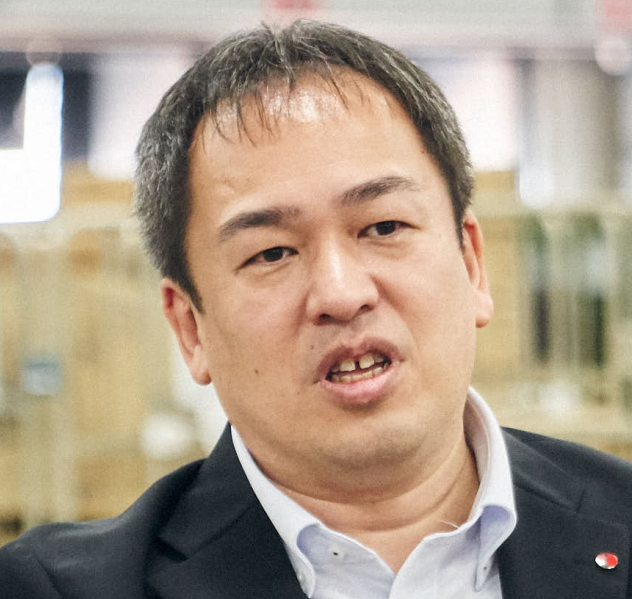
よろしくお願いします。さっそくですが、池澤さんはそもそも物流センターにどのようなイメージを持っていますか?
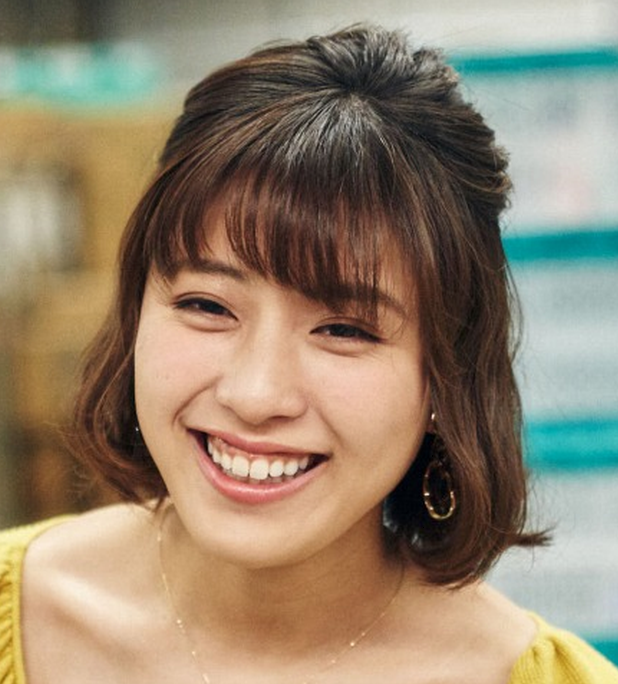
うーん、日常生活で意識したことはあまりなくて、人がたくさんいて棚からモノを出し入れしている…「ザ・倉庫」という感じでしょうか…。
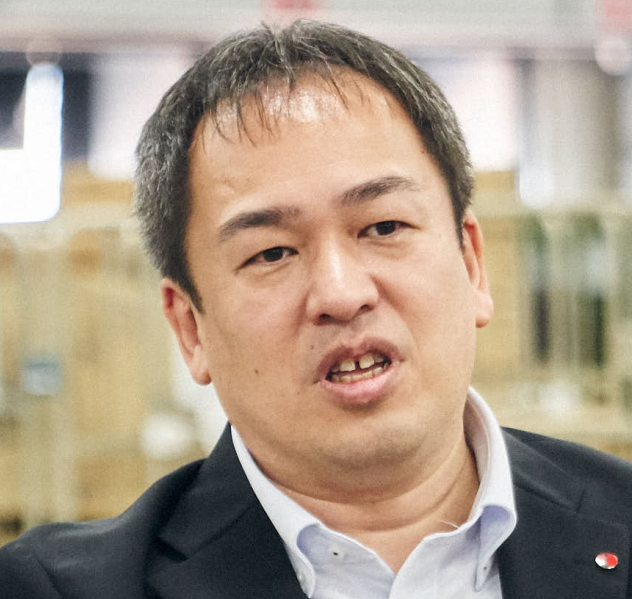
普通はそうですよね。でも弊社のセンターを見ていただければ、イメージがひっくりかえるかもしれませんよ。まずは全体の流れをご説明します。
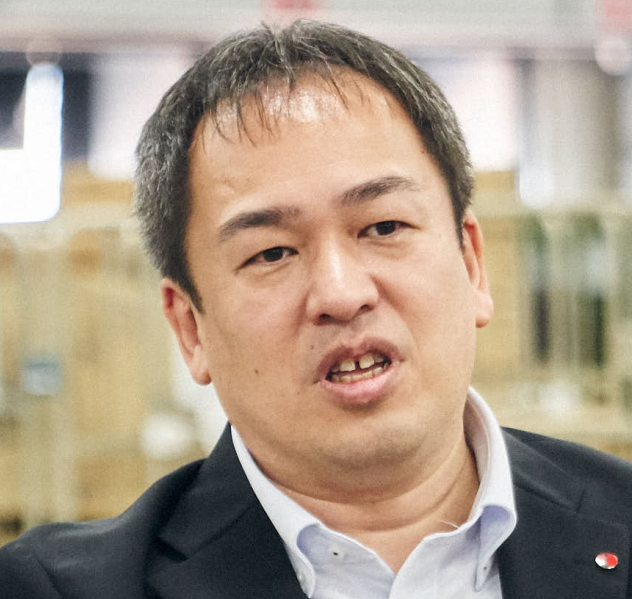
現在日本の労働人口は、急激に減少しています。卸売業でも働き手の減少は免れません。そこで当社はこの労働人口減少の問題に取り組むため、SPAID(スペイド)という次世代型物流システムを自社で研究開発したんです。
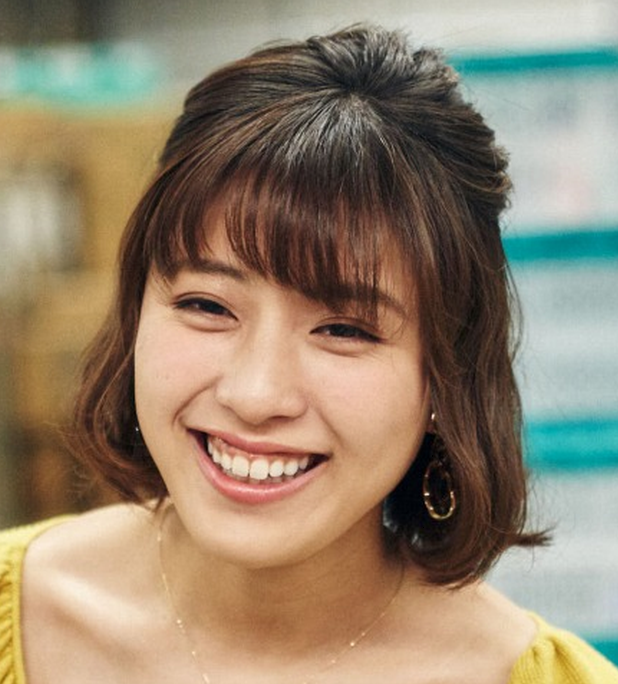
自社でシステムを開発したんですか!
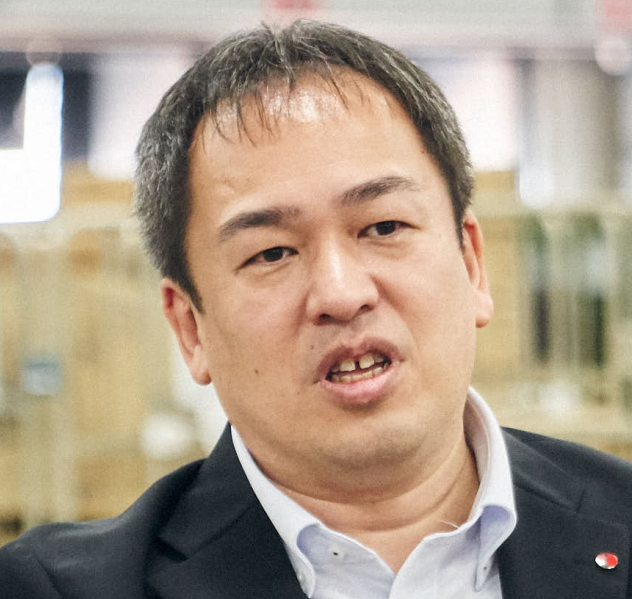
はい。まずはRDCの仕事の全体像を見てみましょう。RDCは「Regional Distribution Center」の略称です。全体の工程は大きく以下のような流れになっています。(クリックで大きく表示されます)
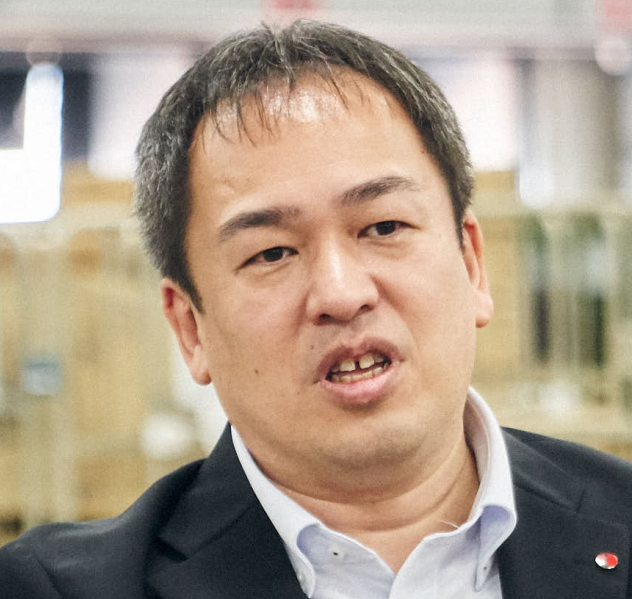
図表には細かく長く書いてありますが、「メーカーから届いた商品を、適切な状態で保管し、小売業の依頼に合わせて出荷する」というのが業務の核です。
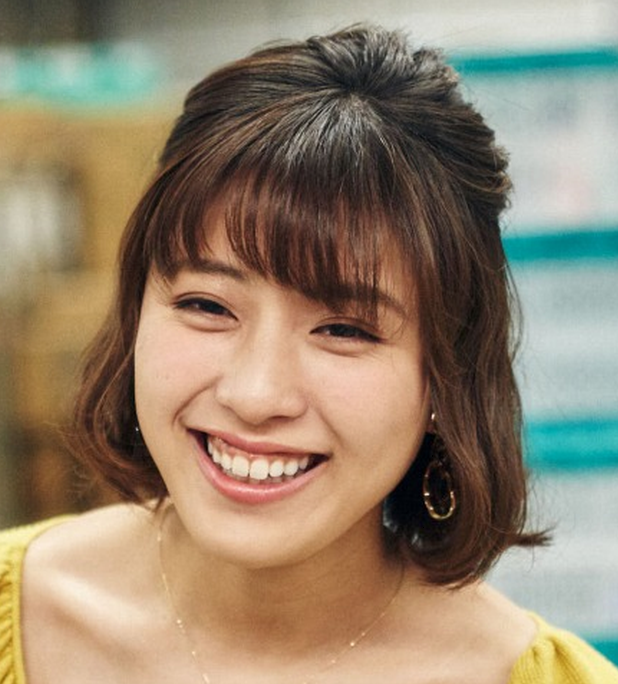
そう説明してもらえるとわかりやすいです!
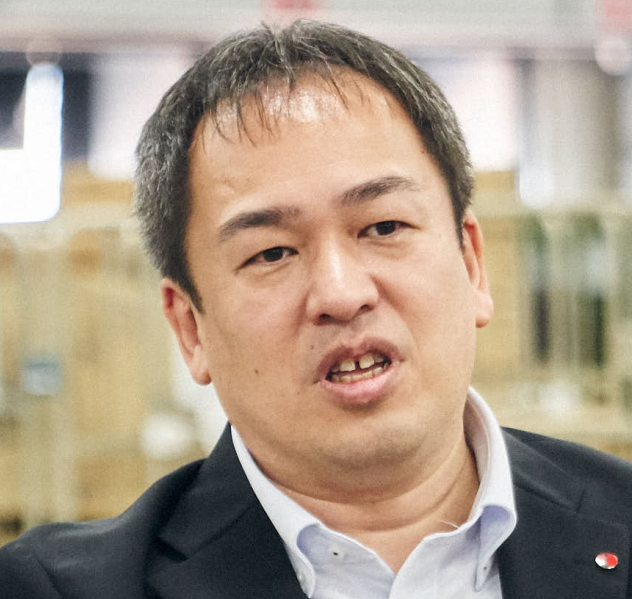
保管時の形状は大きく①パレット、②ケース、③バラの3種類です。このRDCでは、バラの商品は保管トレーというトレーに載せて「トレー自動倉庫」で保管します。
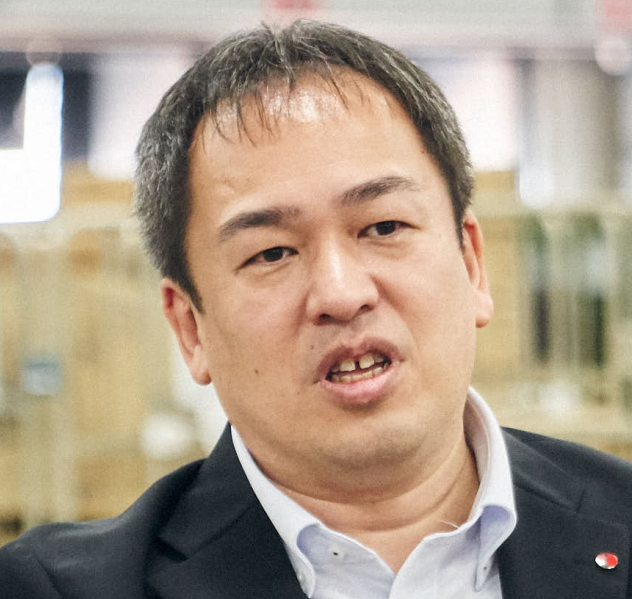
小売業から商品出荷の依頼があると、パレット、ケース、バラの状態で保管している商品が自動的に出庫されて、店舗ごとに仕分けられます。バラの商品はピッキングされて「オリコン」というプラスチック製のケースに入れて出荷します。
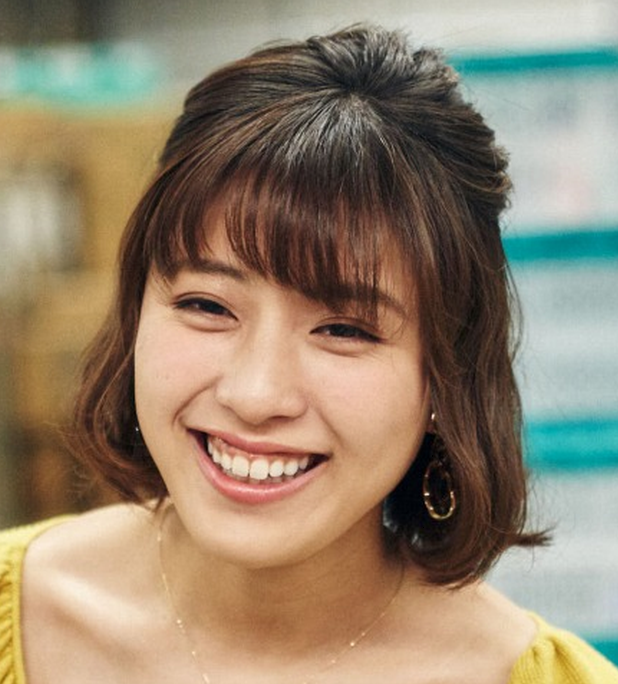
つまりこの、パレット、ケース、トレーに入ったバラの商品、それぞれを適切な状態で保管し、トラックに積み、小売業に届けるのがRDCの仕事なんですね。
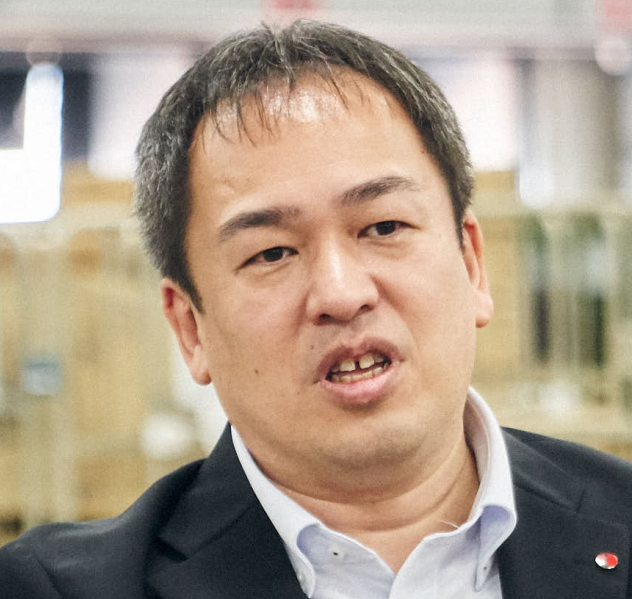
はい。そこで2点改良をした点があって、その1つ目がバラピッキングです。
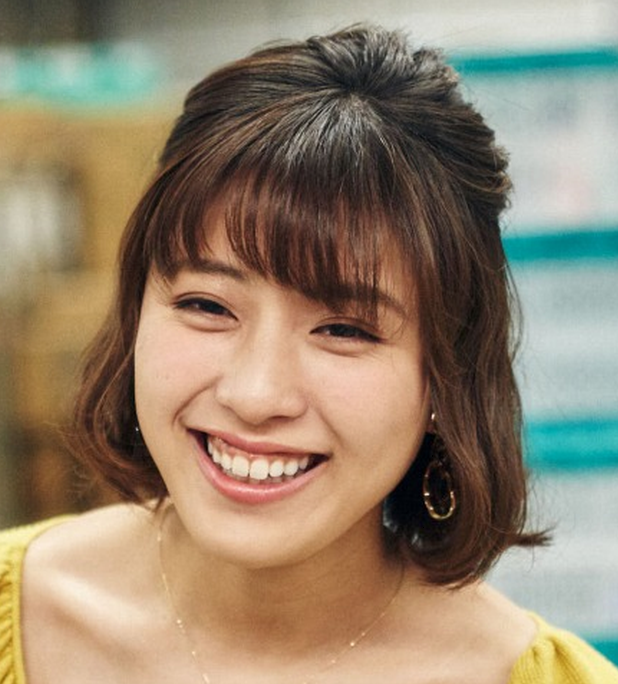
バラピッキング?
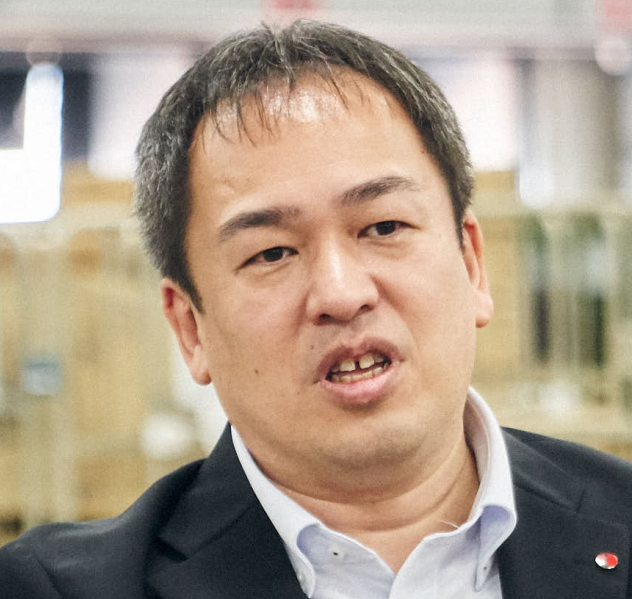
従来のバラピッキングというのは、広大なバラエリアを、作業する人がピッキングカートを押しながら歩行し、棚から商品をピッキングしていたんですね。棚への商品補充も作業者がカートを押しながら歩行して行っていました。
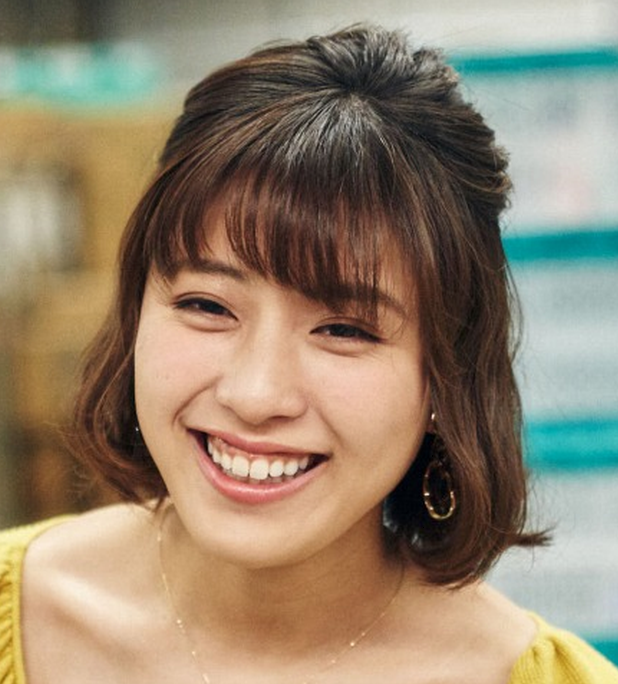
えーー!広い物流センターをカートを押しながら歩いていたんですか!?大きなお店で商品を探してカートを押しながら歩くのって大変ですけど、同じようなことをやっていたわけですね。これはかなり体力がいりそうなお仕事です…。
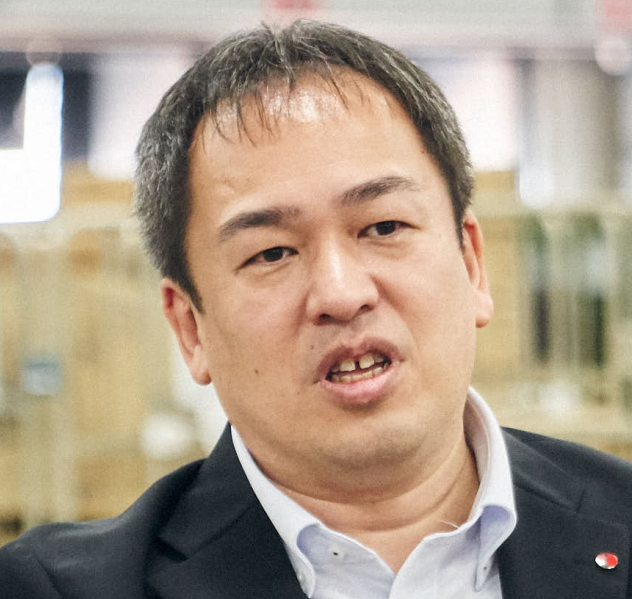
そこで弊社では、人が動くのではなく、逆に商品が動くシステムを開発したんです。これまでは作業時間の半分を「歩行」が占めていたのですが、新方式を採用したことで歩行がなくなり、生産性は従来方式の2倍になっています。
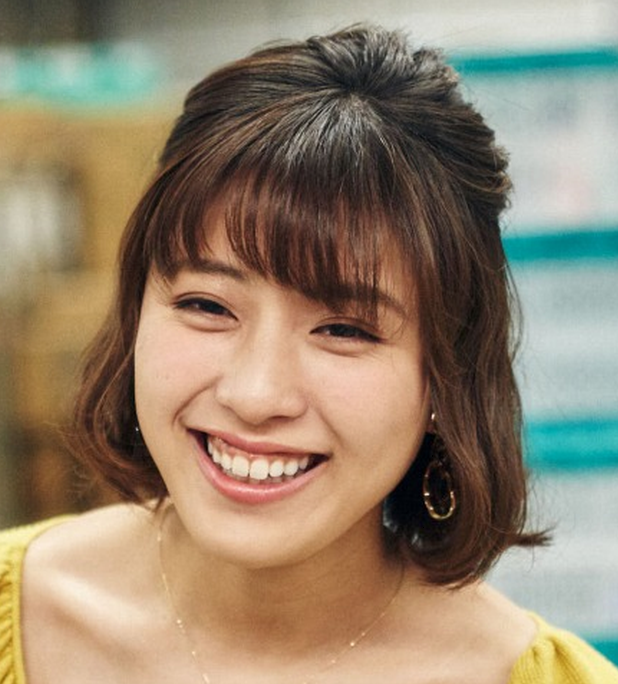
2倍!
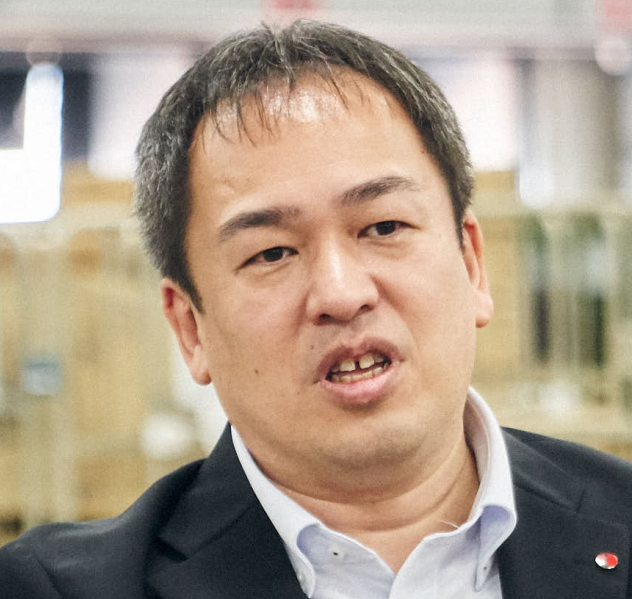
もう一つ大きなポイントとして、これまで人間が行っていたパレット自動倉庫からの出庫作業をロボットを活用することで自動化しています。
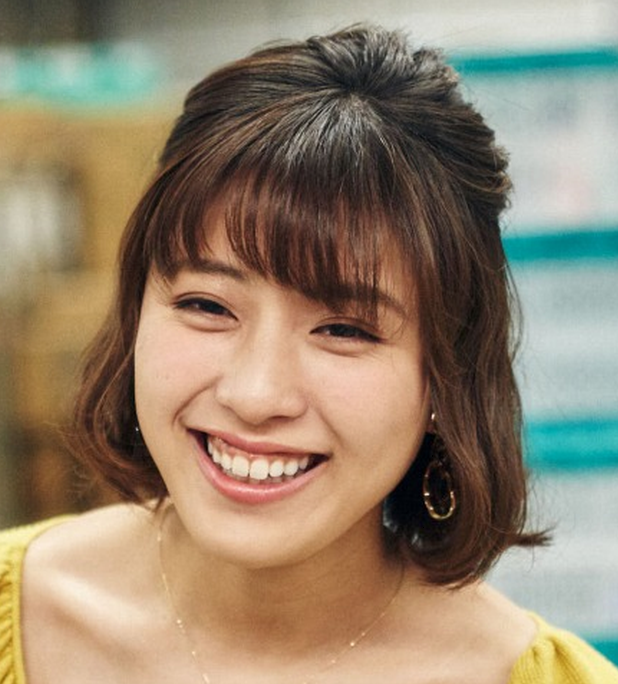
ロボット!めっちゃ自動化進めていますね。実物を見るのが楽しみになってきました。
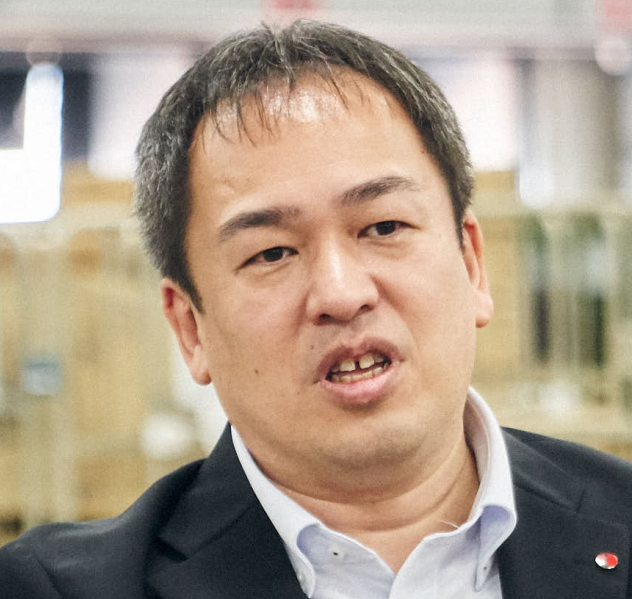
では実際に倉庫に行ってみましょう。
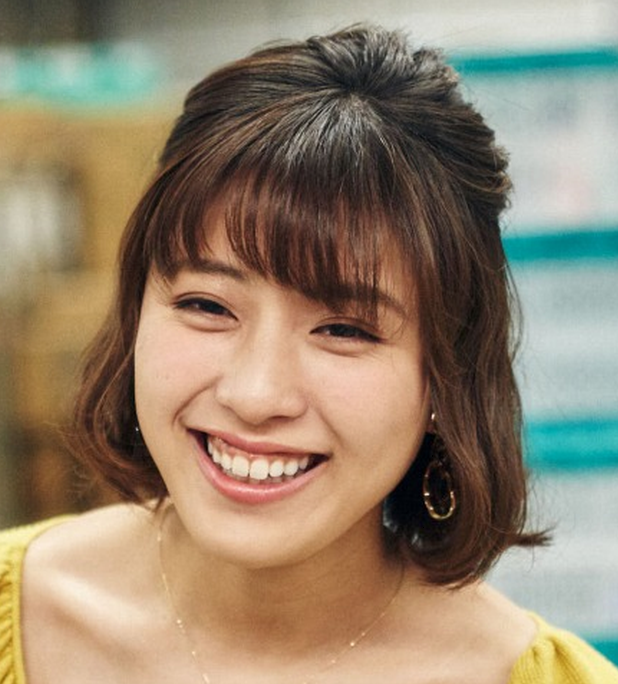
よろしくお願いします!!
入庫エリア:人にやさしい物流倉庫を目指して
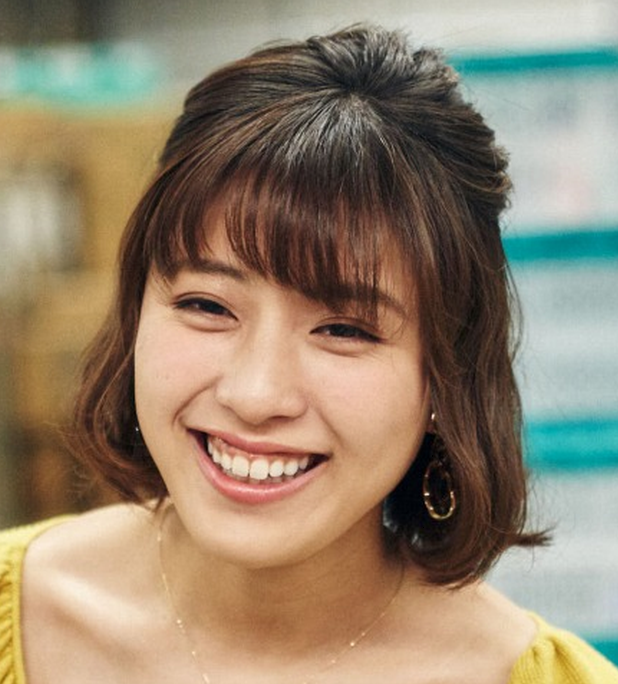
これが物流センターですか。思ったより人が少ないですね!あと、なんだかいい感じの音楽も流れています。
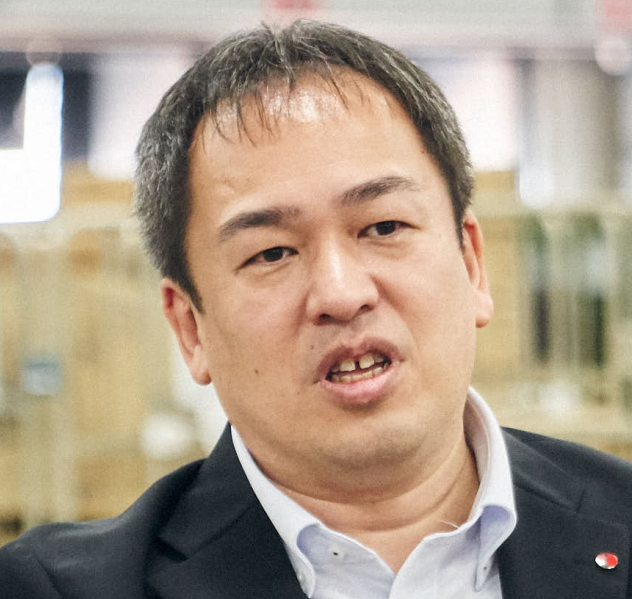
働く人にとってやさしい環境づくりを心掛けていますので、音楽も重要です。
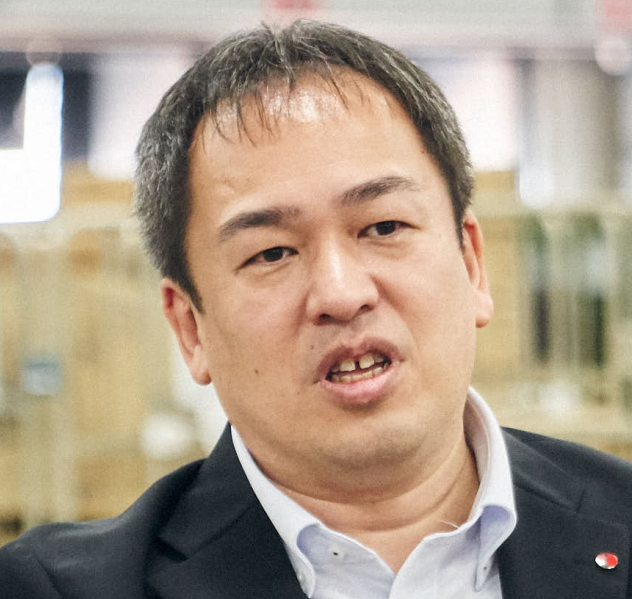
ここは入庫エリアです。メーカーさんから来たトラックが到着します。まずするのが検品作業です。荷物についているバーコードを読み込むと、ケースに何が入っているのかパソコンに表示されるので、入荷予定データと合っているか確認して、OKだったら検品完了となります。
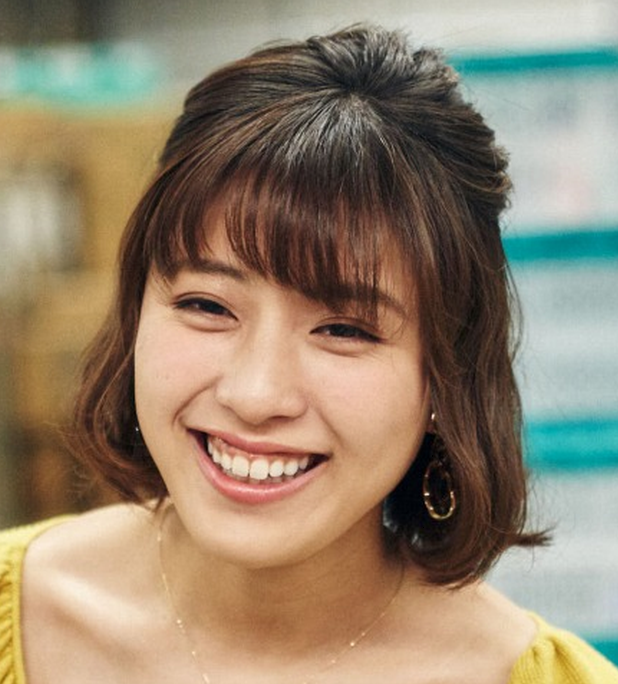
これだけ広いということは、かなり大量の商品が入荷するんですね。
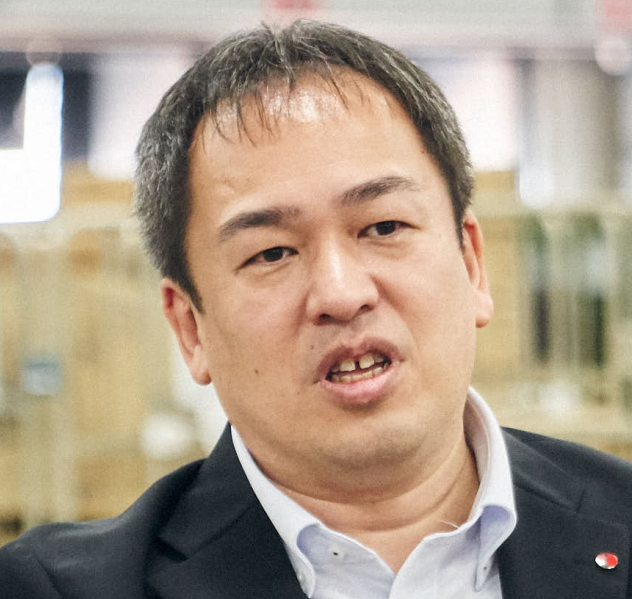
はい。検品完了になるとラベルが印刷されるので、その指示にしたがってフォークリフトで商品を移動します。パレットのまま保管する「パレット自動倉庫」に行くものもあれば、ケースのままで保管する「ケース自動倉庫」に行くものもあります。ケース出荷するものはパレット自動倉庫へ、バラ出荷する商品はケース自動倉庫に行くことが多いですね。
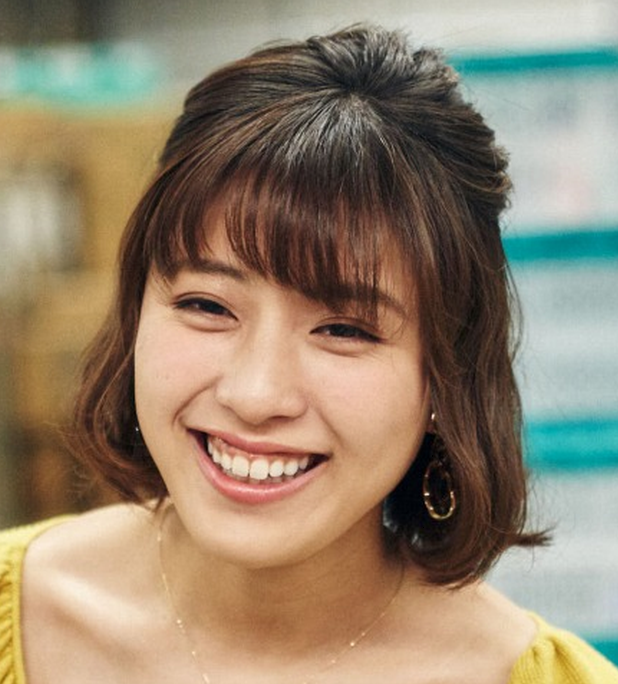
ここで行先が振り分けられるわけですね。
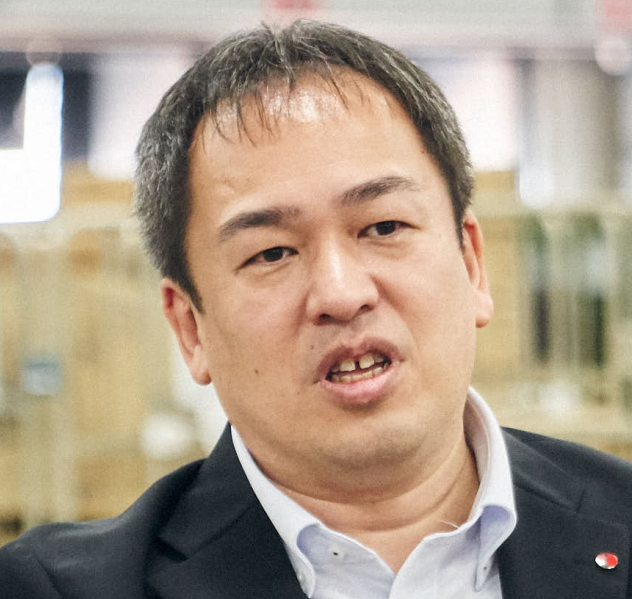
パレットからケースに分ける作業も、作業者の負担を考えて、持ち上げなくても作業できるようにしました。
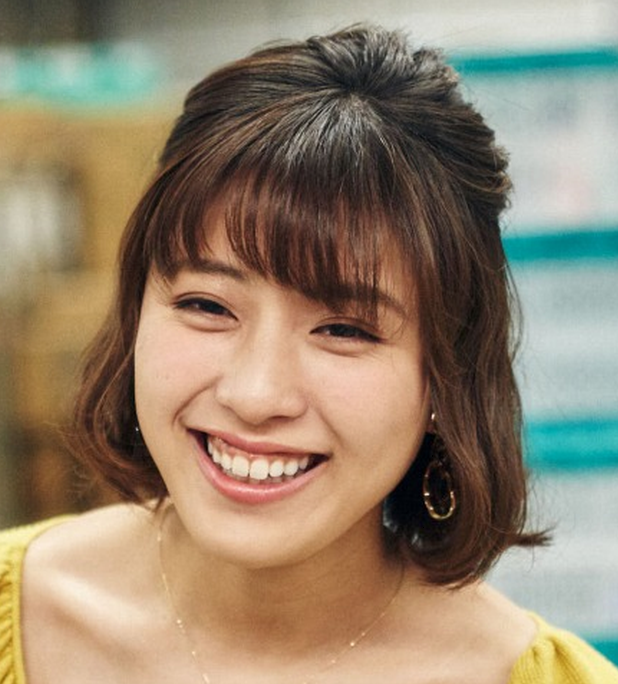
重いもののはずなのに結構楽々ですね。
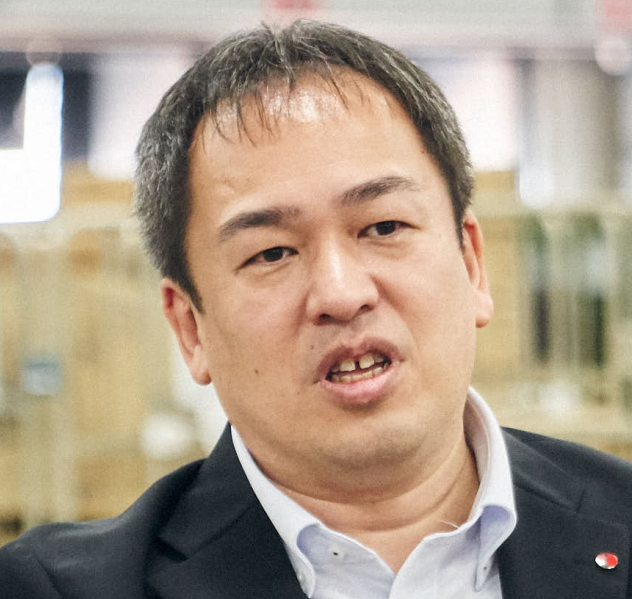
楽だし早いですね。今年11月に埼玉にオープンする新しい物流センターでは検品も自動化する予定です。それと、今は商品をフォークリフトで運んでいますが、ここも自動化します。環状線のようにぐるぐる回っているコンベアの上にパレットを放り込み、所定のところにきたら払い出すというシステムです。
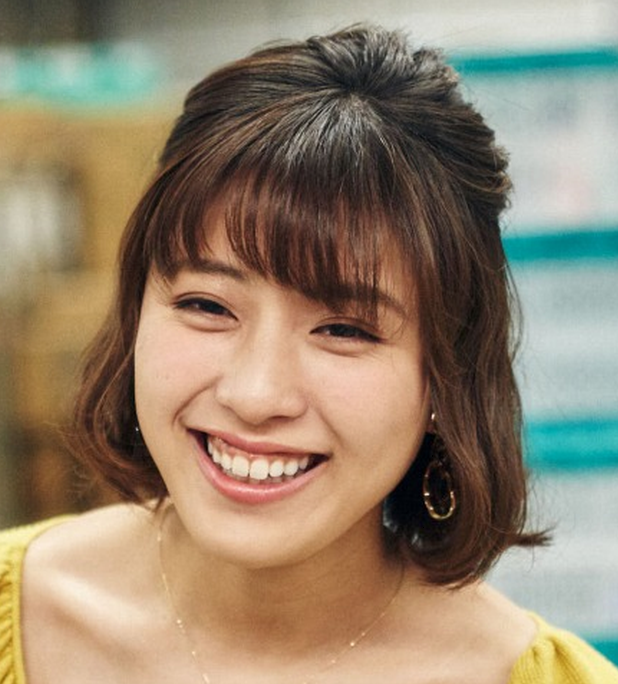
それはヤバイ仕組みですね…。実物を見てみたいです。
パレット自動倉庫:どんな状況でも出荷体制を守り続ける
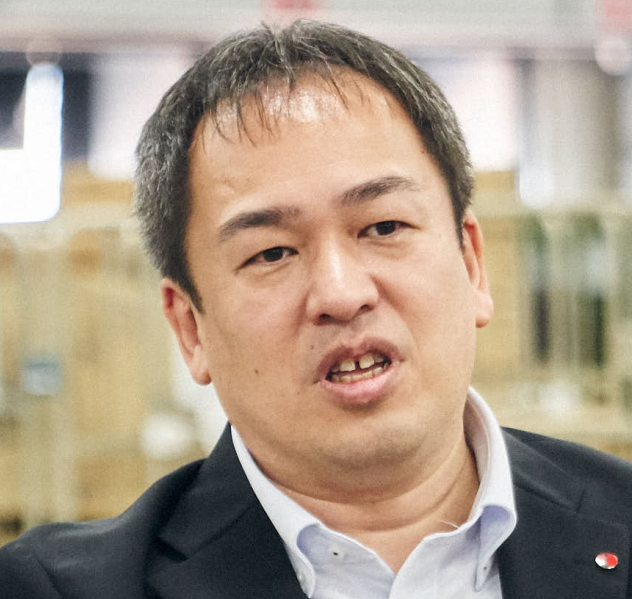
こちらがパレット自動倉庫です。決められた場所にパレットを置くと、クレーンが取りにきて自動で入庫します。
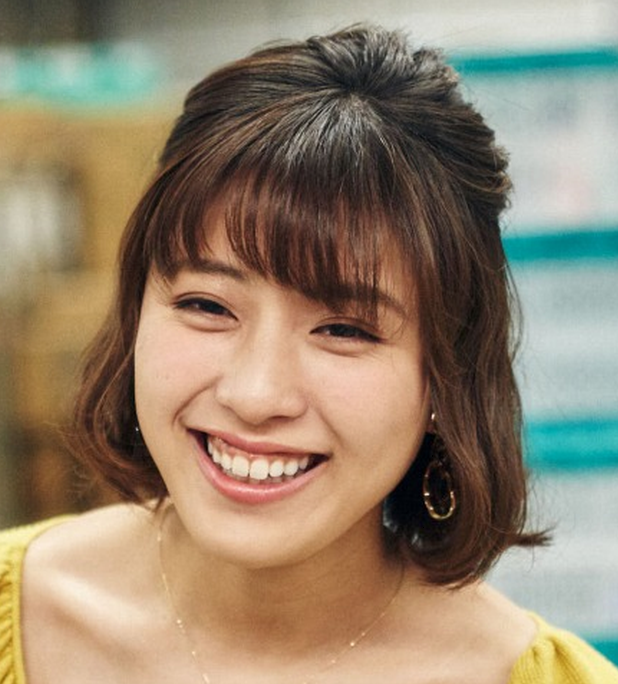
かなり大量に保管できそうです。
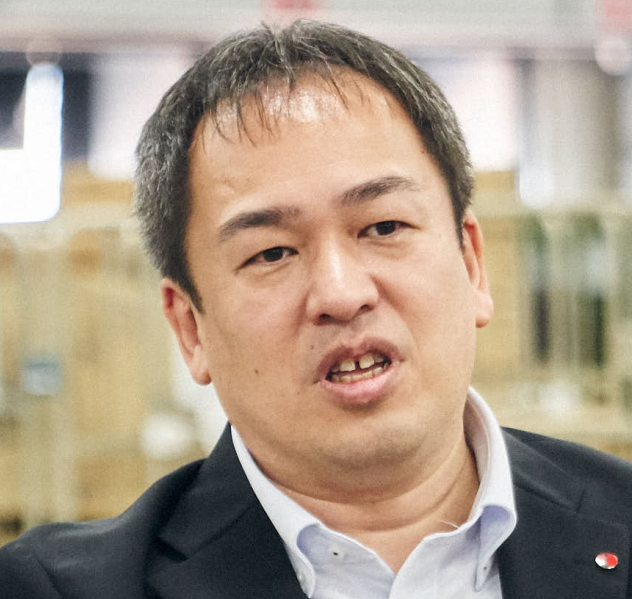
3,872パレットを保管することができますよ。最大10日分の保管量がありますが、高効率運用のために6日間分の保管量で運営をしています。
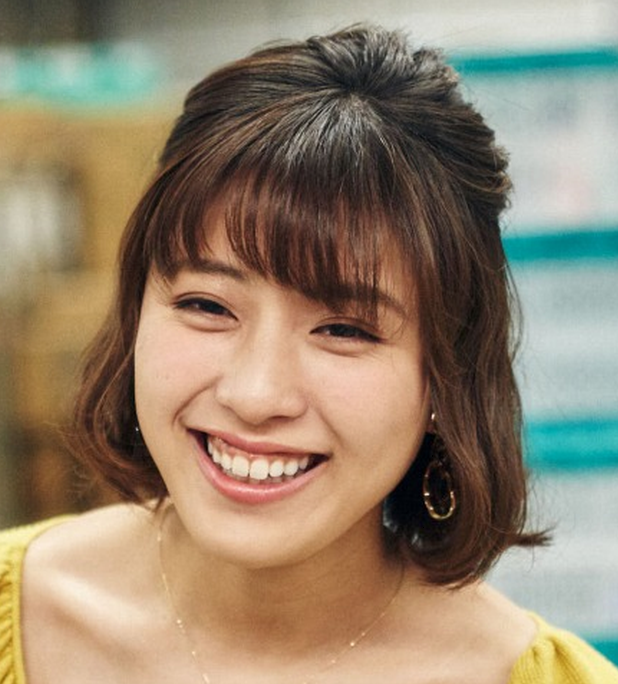
高く積んであるので、揺れには弱そうですが…?
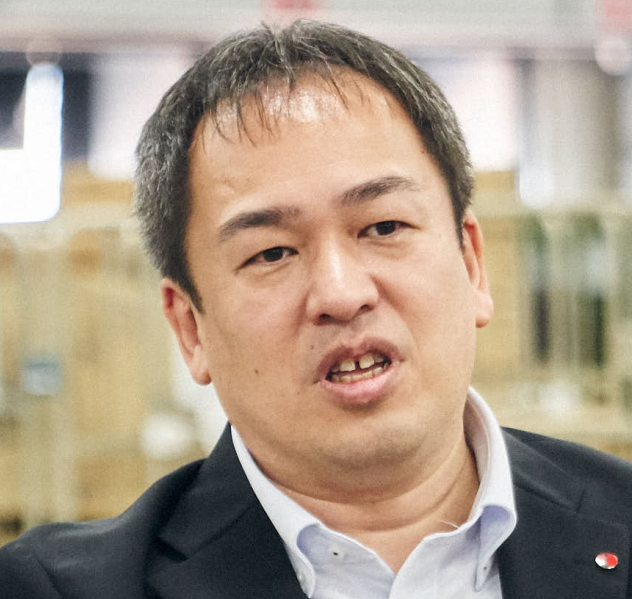
免振装置がついていて、あまり揺れないように設計しています。私たちは生活必需品を扱っているので、地震などで出荷できなくなると、皆さんの暮らしに大きな影響を与えかねません。
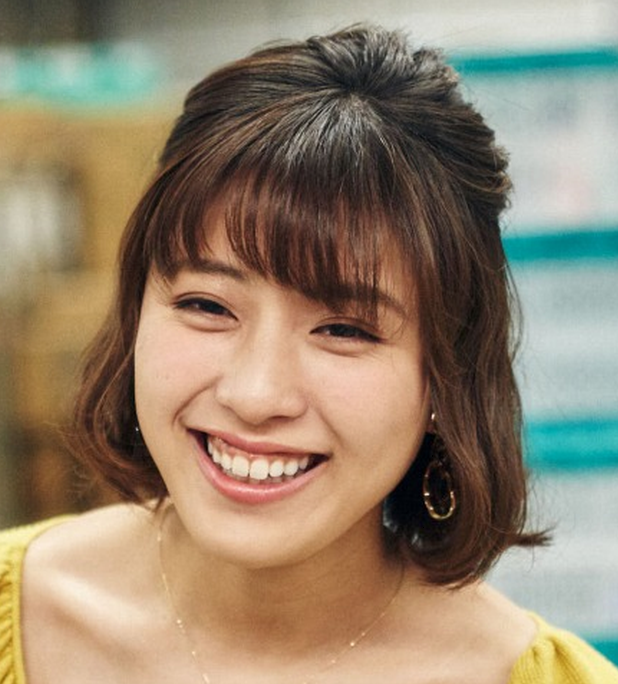
どんな状況でも出荷できる体制を維持しようとなさってるんですね!すごい。
AIケースピッキングロボ:目と脳を持つロボに「柔軟性」を感じる
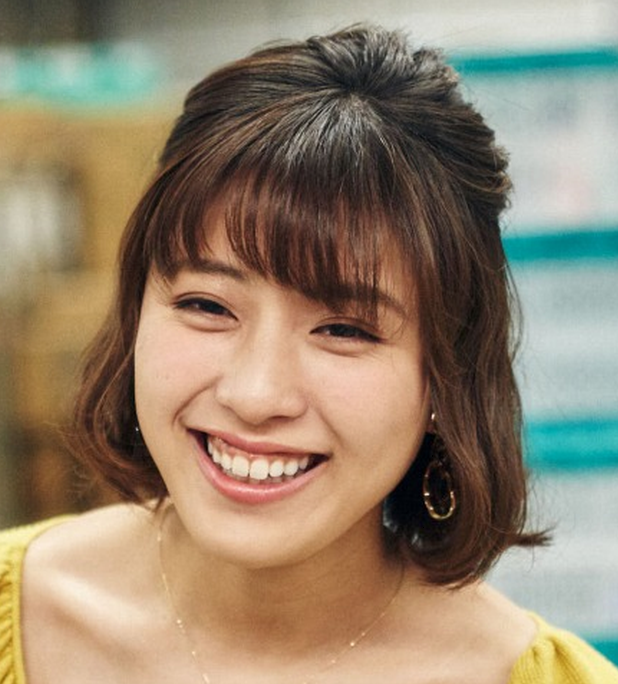
これが噂のロボットですね~。次々とパレットの上のケースを持ち上げています。アームが縦横無尽に移動していて同じ動きがありませんね!!
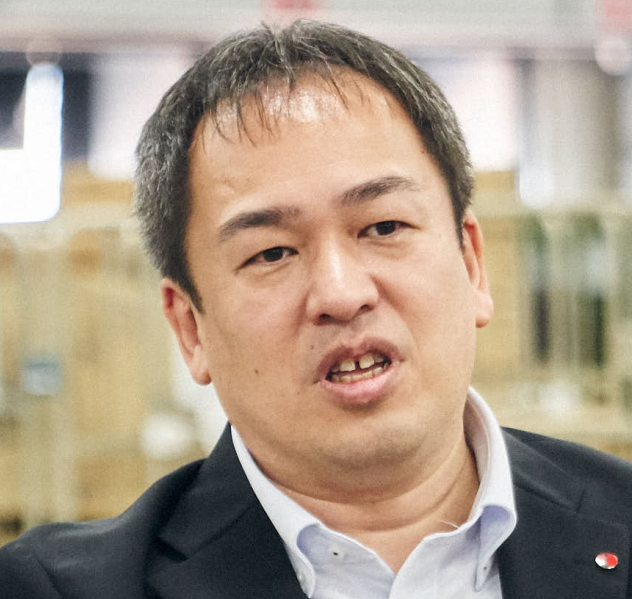
これまでのロボットは決まった商品に対し、同一の動作しかできなかったのですが、このロボットは上部にビジョンセンサーという「目」があって、ケースの形状を認識し、AI(脳)が適切な指示を出すことで、任意の位置から任意の位置へケースを自由に搬送することができるようになったんです。
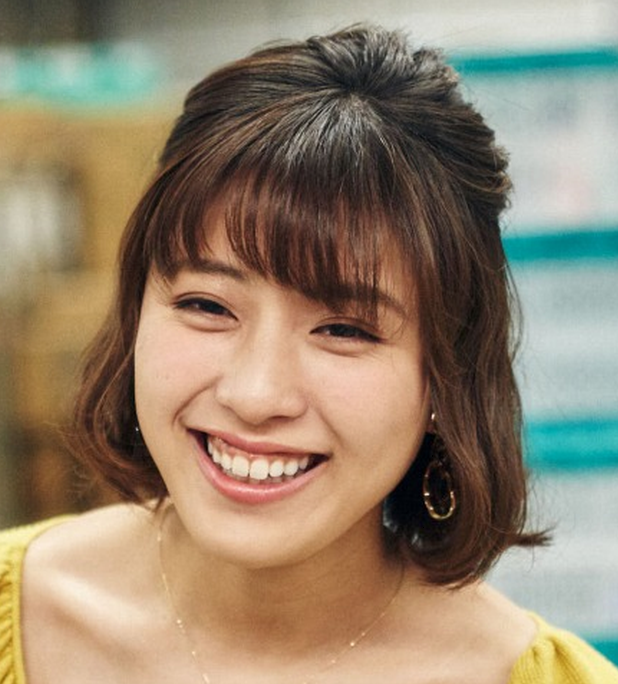
荷物の重量も機械にかかる負荷には関係してくると思うのですが、それはビジョンセンサーだけではわかりませんよね?
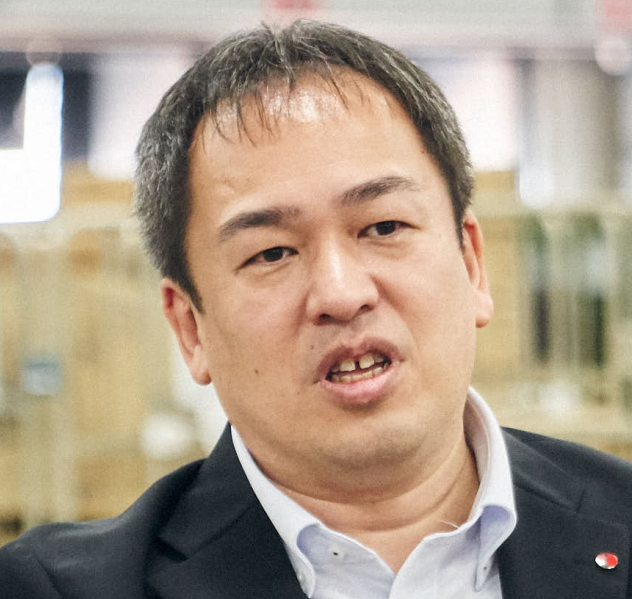
新商品が出てきたときに、あらかじめケースの形や重量を人間がマスタに登録しておくんです。ビジョンセンサーがケースを認識したときに、マスターに登録されている荷姿や重量の情報と紐づけて、最適な搬送方法をリアルタイムで判断します。
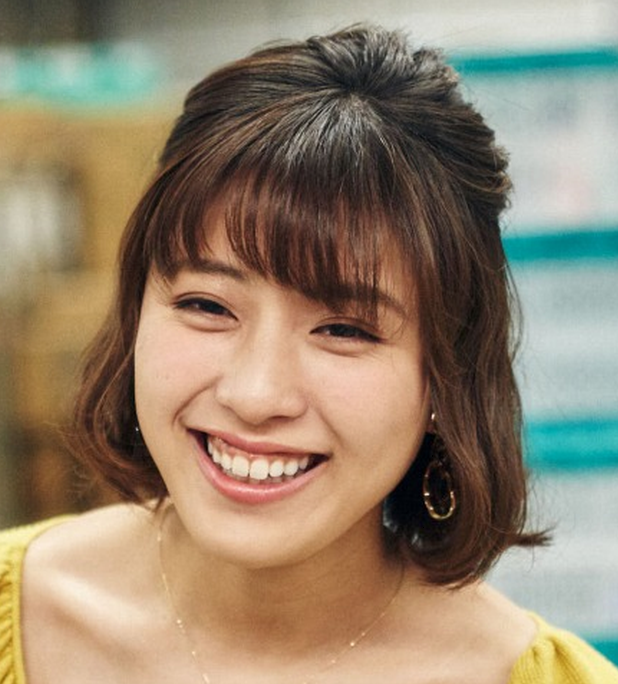
ケースを持ち上げているのは吸盤ですか?
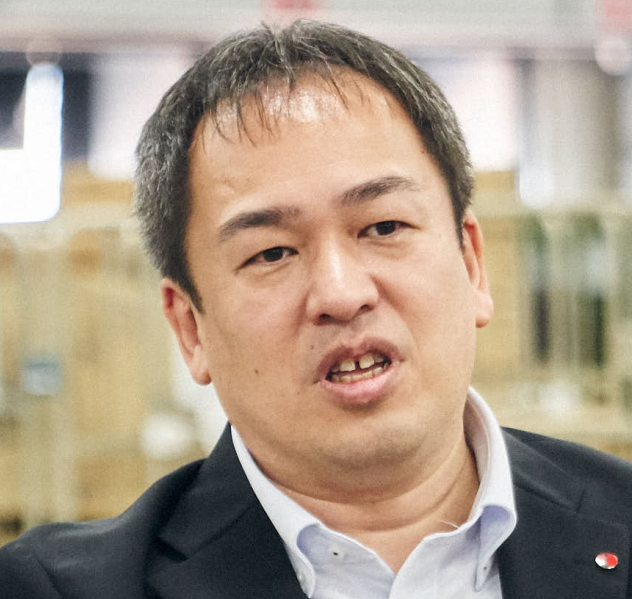
はい。真空状態にして吸い上げています。
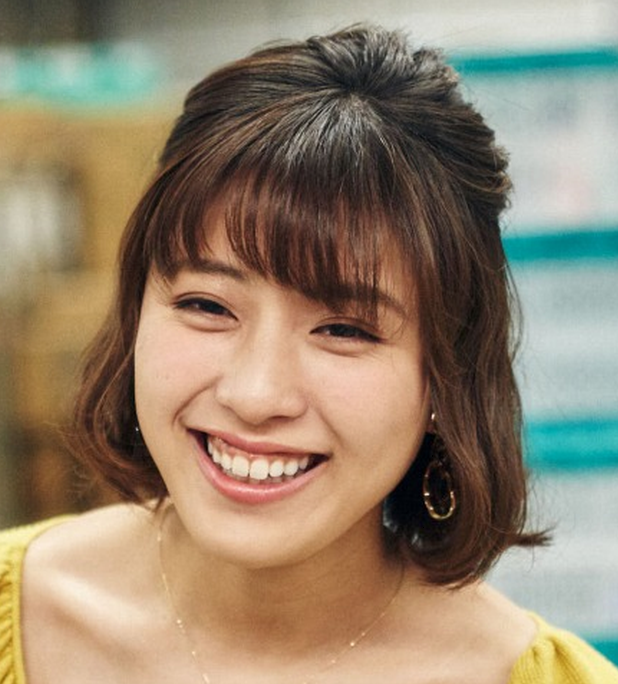
次から次へといろいろな形状のケースを運んでいます。さっきはかなり大きなケースを運んでいましたが、今度はとても小さなケース。賢いですね!ロボットの柔軟性を感じますね…。
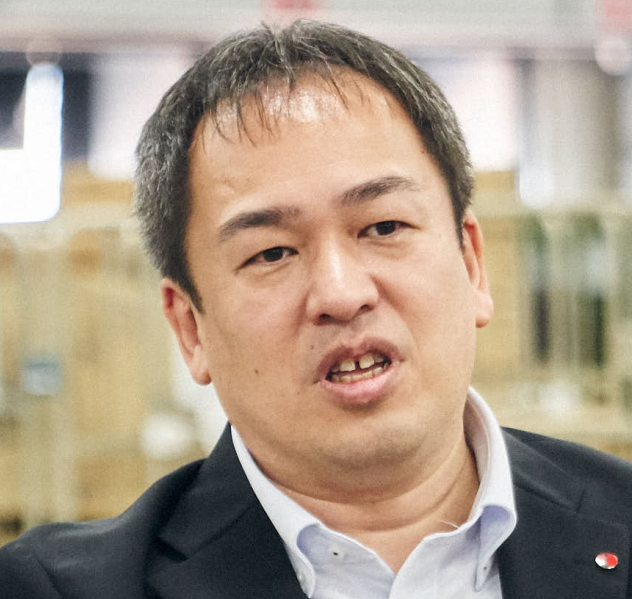
昔はこれも全部人の手でやっていたんですよ。私も新人研修でやったことがありますが、腰がもたなくて途中でギブアップしました(苦笑)。
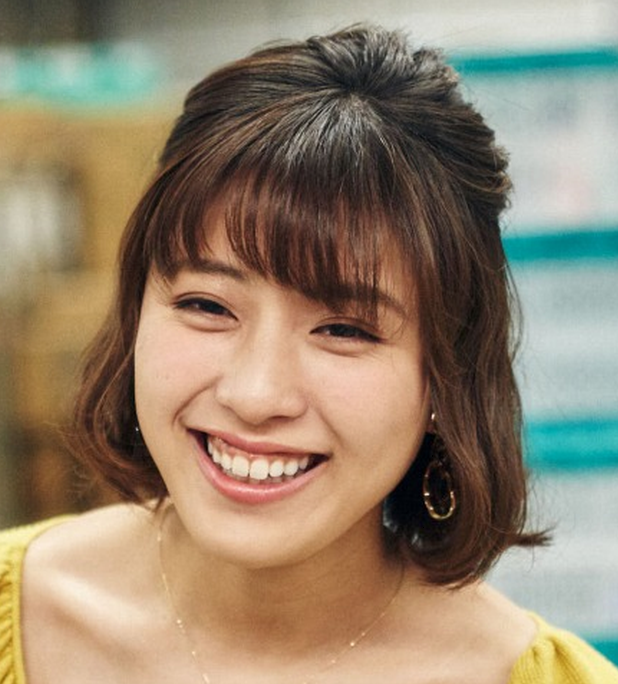
これは本当に大変そうです。ロボットを導入したことでどれぐらい効率化されたんですか?
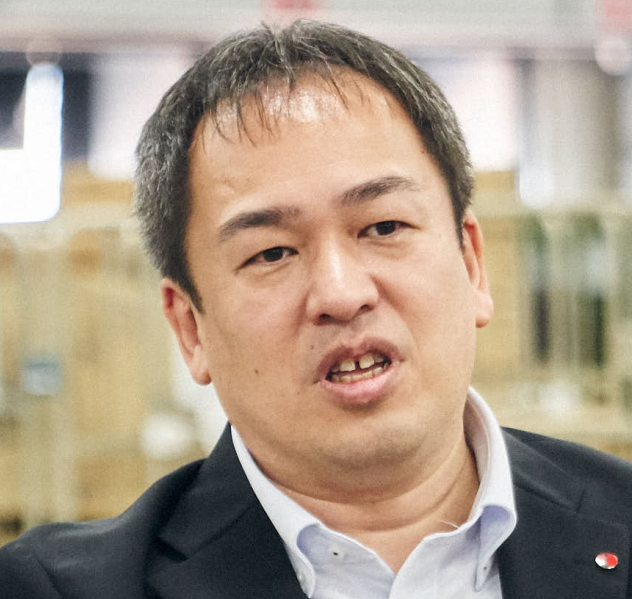
人が作業すると1時間に150ケースをさばくことができるんですが、このロボットを使うと1時間に600ケース対応できますので4倍です。人はどうしても疲れてしまいますが、ロボットは疲れませんので。
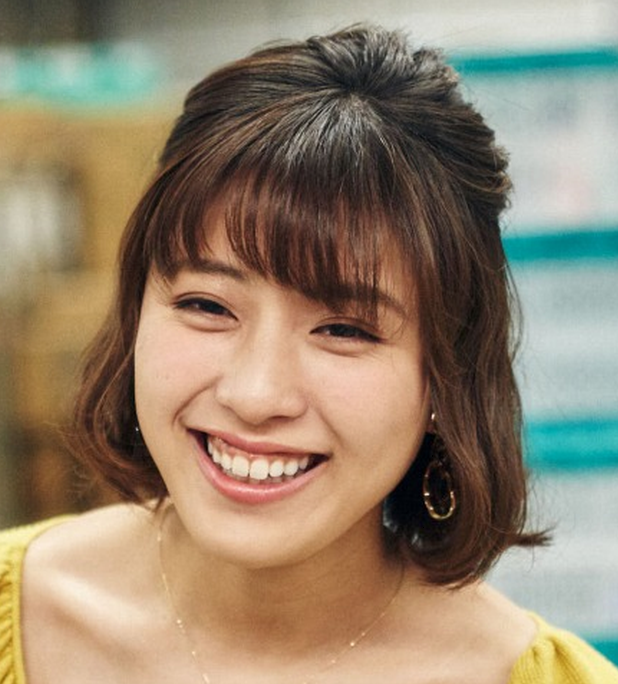
人とロボットで分担をした方がいいですね。お互い得意な分野をすると幸せになれそうです。
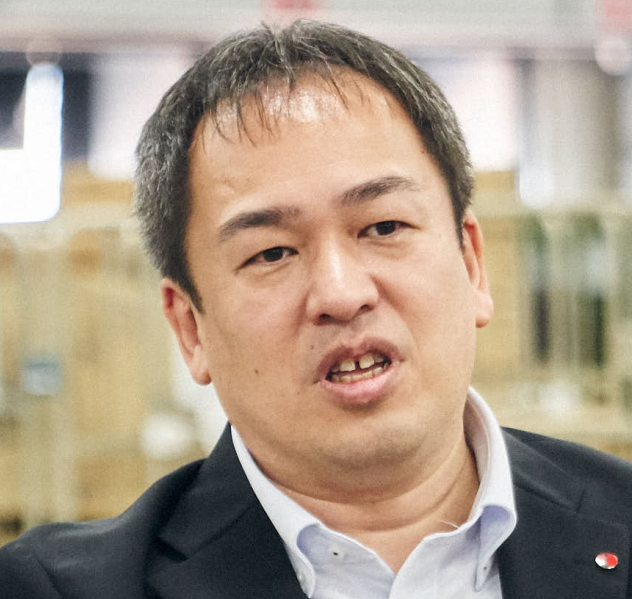
では次の工程に向かいましょう!
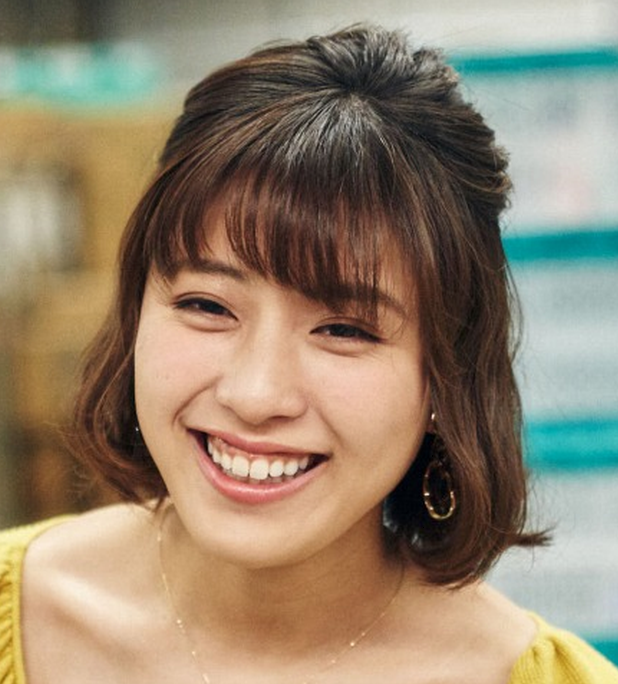
はい!ってこんなところ通るんですか~~!?(悲鳴)
後編に続く